- PRO Courses Guides New Tech Help Pro Expert Videos About wikiHow Pro Upgrade Sign In
- EDIT Edit this Article
- EXPLORE Tech Help Pro About Us Random Article Quizzes Request a New Article Community Dashboard This Or That Game Popular Categories Arts and Entertainment Artwork Books Movies Computers and Electronics Computers Phone Skills Technology Hacks Health Men's Health Mental Health Women's Health Relationships Dating Love Relationship Issues Hobbies and Crafts Crafts Drawing Games Education & Communication Communication Skills Personal Development Studying Personal Care and Style Fashion Hair Care Personal Hygiene Youth Personal Care School Stuff Dating All Categories Arts and Entertainment Finance and Business Home and Garden Relationship Quizzes Cars & Other Vehicles Food and Entertaining Personal Care and Style Sports and Fitness Computers and Electronics Health Pets and Animals Travel Education & Communication Hobbies and Crafts Philosophy and Religion Work World Family Life Holidays and Traditions Relationships Youth
- Browse Articles
- Learn Something New
- Quizzes Hot
- This Or That Game New
- Train Your Brain
- Explore More
- Support wikiHow
- About wikiHow
- Log in / Sign up
- Hobbies and Crafts
- Woodworking

How to Build a Plywood Boat
Last Updated: August 10, 2021 References
wikiHow is a “wiki,” similar to Wikipedia, which means that many of our articles are co-written by multiple authors. To create this article, 11 people, some anonymous, worked to edit and improve it over time. This article has been viewed 79,650 times. Learn more...
Building your own plywood (stitch and glue) boat is a low cost and light weight alternative to spending $10,000+ on an expensive commercially built boat that is difficult to trailer, very heavy, and guzzles gas. Online research, low-cost study plans, and talking to someone who has built their own boat, will help you decide which boat is best for you.

- YouTube has many good how-to lay fiberglass videos; however finding someone local who lays fiberglass is the best way to get some hands on training. There are dozens of good marine supply stores online that will sell you a quality fiberglass and your boat plans should have the amount (length in yards) and weight (ounces) of cloth you will use on your boat.

Expert Q&A
- This information is only that a quick overview of boat-building and not in-depth Coast Guard approved advice. Thanks Helpful 0 Not Helpful 0
Things You'll Need
- Skilsaw w/a good blade
- 5' orbital sander
- Belt sander
- Various knives
- Bristle brushes
- Mixing cups
- Any other items in your boat plans
You Might Also Like

- ↑ http://www.fao.org/3/y5649e/y5649e00.htm
- ↑ https://www.woodenboat.com/marine-plywood
- ↑ https://www.youtube.com/watch?v=8GQxtaqlAHs
- ↑ https://www.youtube.com/watch?v=9jHUI0CiYbs
- ↑ https://www.boatus.com/magazine/2017/april/10-steps-to-the-perfect-topside-paint-job.asp
About This Article
- Send fan mail to authors
Did this article help you?

Featured Articles

Trending Articles

Watch Articles

- Terms of Use
- Privacy Policy
- Do Not Sell or Share My Info
- Not Selling Info
Don’t miss out! Sign up for
wikiHow’s newsletter
Free Shipping On All Orders!
- Epoxy Resins
- Polyester Resin
- Urethane Resins
- Epoxy Project Supplies
- Antifouling Paints
- Topside Paints
- Thinners & Solvents
- Paint Supplies
- Wood Oils & Finishes
- Wood Finishing Supplies
- Cleaning & Polishing
- Accessories
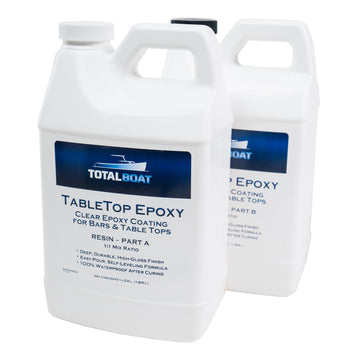
Table Top Epoxy
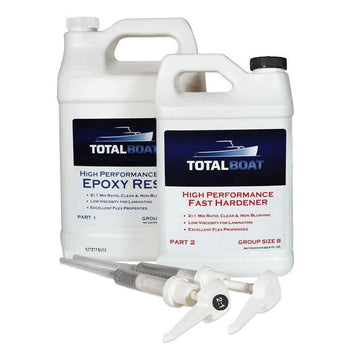
Clear High Performance Epoxy Kits
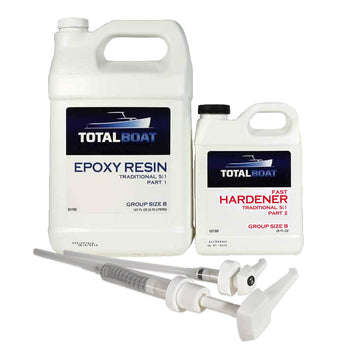
5:1 Traditional Epoxy Resin Kits
- Thinners & Solvents
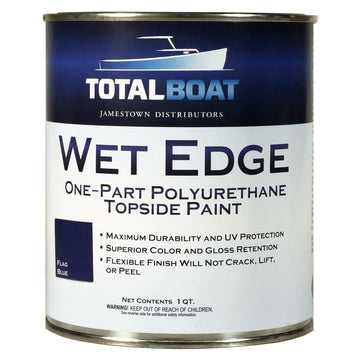
Wet Edge Topside Paint
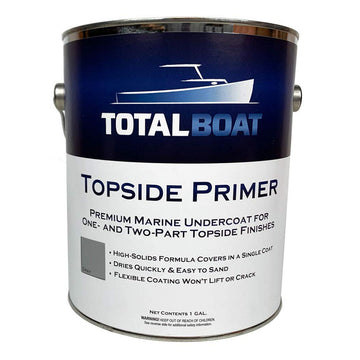
Premium Marine Topside Primer
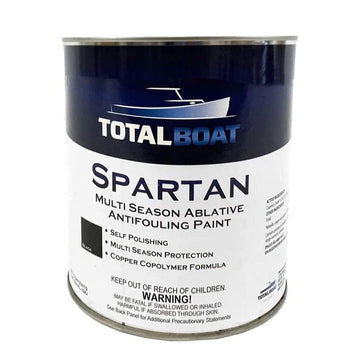
Spartan Multi-Season Antifouling Paint
- Wood Finishes
- Wood Oils & Finishes
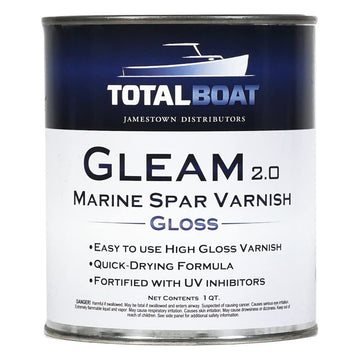
Gleam 2.0 Marine Spar Varnish
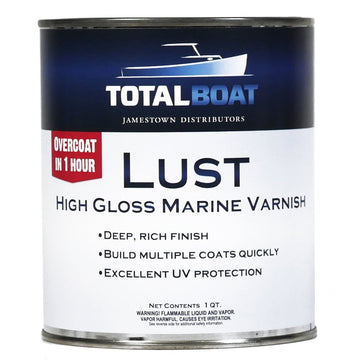
Lust Rapid Recoat Marine Spar Varnish
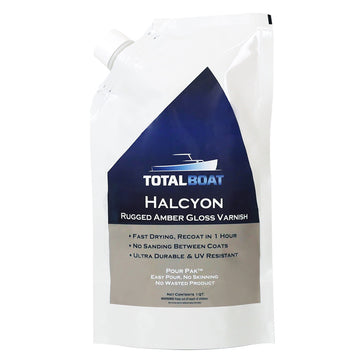
Halcyon Water-Based Marine Varnish
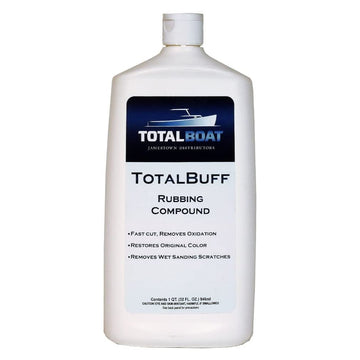
TotalBuff Rubbing Compound
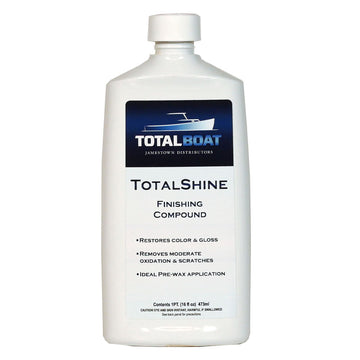
TotalShine Finishing Compound
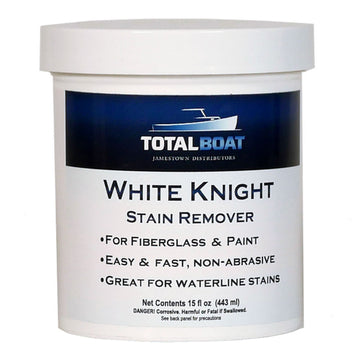
White Knight Fiberglass Stain Remover
- TotalBoat Gear
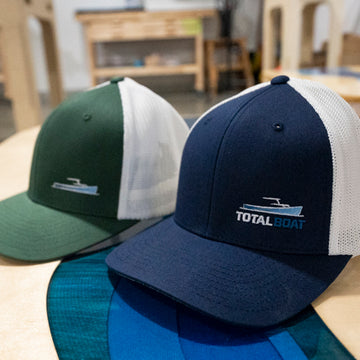
FlexFit Fitted Mesh Back Baseball Cap
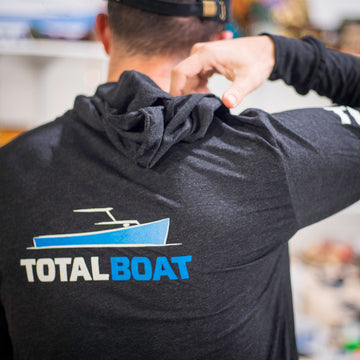
Men’s Long Sleeve T-Shirt Hoodie
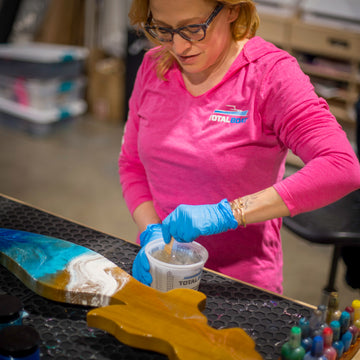
Women’s Long Sleeve T-Shirt Hoodie
FREE SHIPPING with a minimum puchase of $1,200.00 You are $10.00 away from your free shipping!
Shipping, taxes, and dicount codes calculated at checkout.
The Ultimate 5-Day DIY Plywood Boat Build
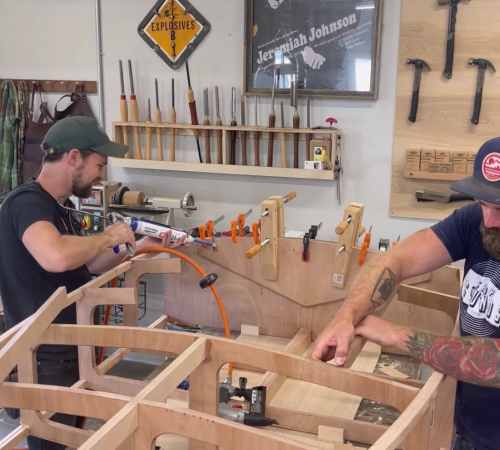
When Jason Hibbs of Borbon Moth Woodworking and Michael Alm of Alm Fabrications asked TotalBoat for support during their 5-day, no-real-plan boat build, we knew we needed to send a lot of Thixo Fast and also that we might have our hands full. These two talented woodworkers could create intricate plans and pull off a complicated piece of furniture without issue – but the boat building provided an extra challenge – as we know. Without square corners and nary a straight line, the duo set out to work their way through the build of the cocktail class racer and take it step-by-step, figuring out each challenge as they arose. Jason’s previous boat-building victory was his drift boat that he’s enjoyed using in his native Oregon waters. This could only mean that Jason was aware of some of the challenges that would come. But knowing Jason, we thought that the impossibility of the project and his can-do approach was worth the risk. Part 1 of this build series is a fun glimpse into these woodworker’s brains as they tackle the tough parts of boat building like constructing the ribs with the correct angles and making progressive bevels. They sort through each step and find solutions that might not be how Louis Sauzedde or Steve from Acorn to Arabella may do it, but we had confidence that they would succeed, albeit a bit differently. And that can be fun. Tune in for Part 1 and see how they fare with the toughest parts of building a wooden boat. Now go over to Michael’s channel and check out his video of the same project. Give them both a “subscribe” while you’re there and you’ll be in on their awesome content and crazy builds!
Leave a comment
Related articles.
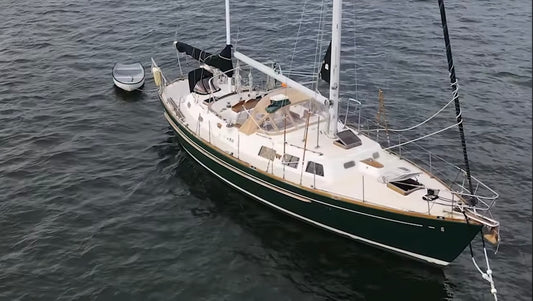
Refitting a Sailboat and Fixing Leaks with Ran-Day
Randall, or as you may know him as Ran-Day, from Yacht Hunters is an avid sailor and cyclist, embarking on a monumental project: refitting and modernizing an old Scheel 45...
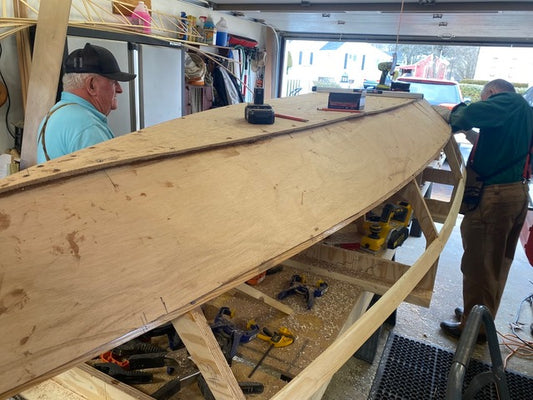
Boat Building with Richard Honan and Friends
There's something magical about Sundays, isn't there? It's a day when time seems to slow down just enough for us to appreciate the simple joys of life. For TotalBoat Ambassador,...
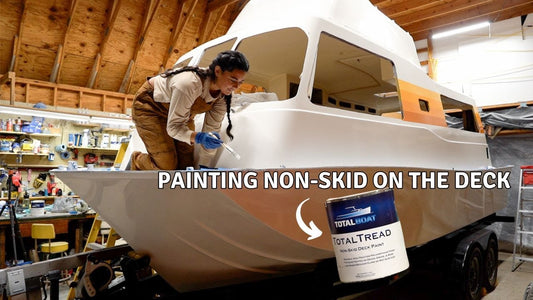
TotalTread Transforms Decks on Slow Car Fast Ho...
Danielle and Tommy, from Slow Car Fast Home, are the proud owners of a 1978 SeaCamper - a 24ft trailerable houseboat that they are bringing back to life with a...
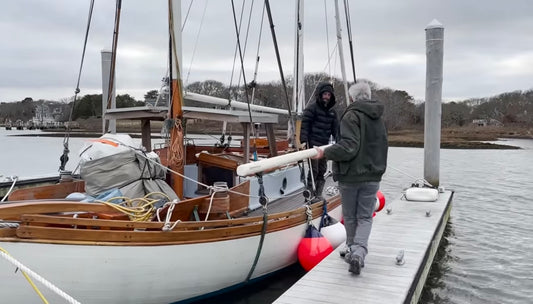
Arabella Gets a New Mizzen Boom!
Welcome back aboard Arabella! A few episodes back on Acorn to Arabella, Arabella’s mizzen boom broke on their trip to Harwich Port, MA. And, with Robin’s dad's shop just a...
- Choosing a selection results in a full page refresh.
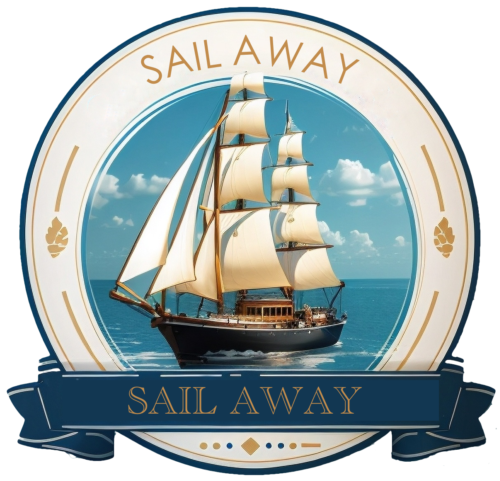
The Ultimate Guide on How to Build a Sailboat – Step by Step Instructions and Expert Tips
Alex Morgan
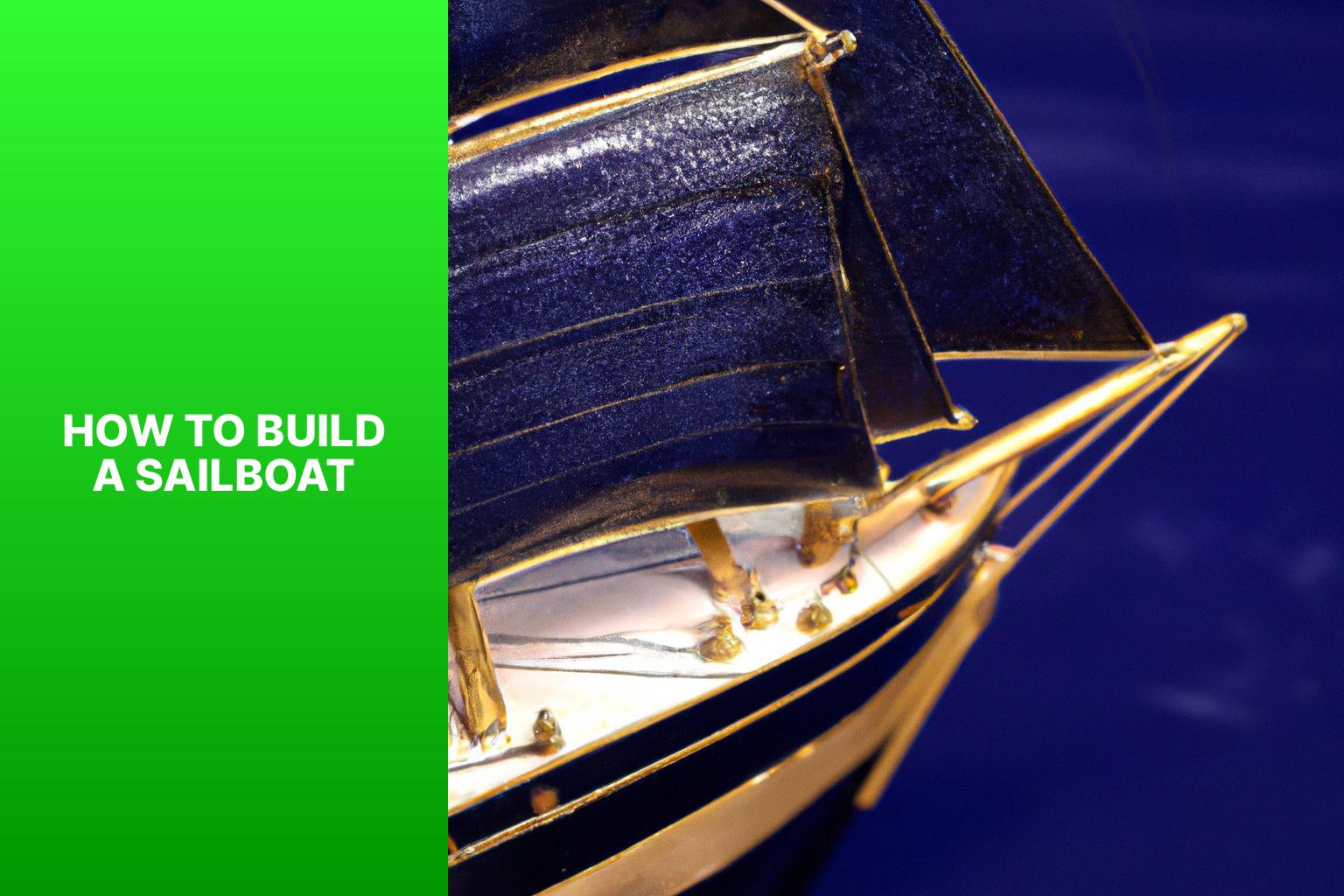
Building a sailboat can be a rewarding and fulfilling project for those with a passion for sailing and craftsmanship. Whether you’re an experienced builder or a novice, constructing your own sailboat allows you to customize it to your specific needs and preferences. This comprehensive guide will take you through the step-by-step process of building a sailboat.
To start, gather the necessary tools and materials required for the construction. The specific tools needed may vary depending on the design and complexity of the sailboat. Basic tools such as measuring tape, saws, drills, and sandpaper are commonly used during the building process. specialized tools like a planer, router, and clamps may be required for more intricate details.
In terms of materials, you’ll need various types of wood for the hull, frames, and deck, as well as epoxy resin, fiberglass cloth, and marine-grade plywood. Other materials like stainless steel screws, bolts, and fittings will be needed for assembling and securing the different components of the sailboat.
Choosing the right sailboat design is a crucial step in the building process. Consider factors such as the intended use, sailing conditions, and your own level of experience. Factors like the boat’s size, stability, and performance characteristics should also be taken into account.
Before diving into the construction, it’s important to prepare a suitable building site. This includes having enough space to work on the boat, a clean and organized area, and proper ventilation. A sturdy workbench or support system is necessary for holding the boat’s components during assembly.
The hull of the sailboat is a fundamental part of the construction process. Follow a step-by-step process for constructing the sailboat hull, which involves shaping and assembling the frames, planking the hull with marine-grade plywood, and applying epoxy resin and fiberglass for added strength and durability.
Once the hull is completed, it’s time to install the sails and rigging. Properly attaching and rigging the sails is essential for optimal performance and maneuverability. This includes setting up the mast, boom, and other rigging components in accordance with the sailboat’s design specifications.
Next, focus on essential systems and finishing touches. Install electrical and plumbing systems as per your requirements, ensuring they are safe and efficient. Applying finishes and sealants to the boat’s exterior not only enhances its appearance but also protects it from the elements.
Before launching your sailboat, conduct safety checks to ensure everything is in proper working order. Inspect the hull, rigging, and other components for any potential issues. Once you have done all the necessary checks, follow tips for a successful sailboat launch, ensuring a smooth transition from construction to the open water.
By following this guide, you’ll be well-equipped to embark on the exciting journey of building your own sailboat. With careful planning, attention to detail, and patience, you’ll soon have a vessel that reflects your skills and passion for sailing.
Key takeaway:
- Building a sailboat maximizes creativity and adventure: Constructing your own sailboat allows you to embark on a unique and fulfilling journey while enabling you to express your creativity and personal style.
- Gathering the right tools and materials is crucial: Having the necessary tools and materials is essential for building a sailboat successfully. Ensure you have the appropriate tools and high-quality materials to construct a sturdy and reliable sailboat.
- Choosing the right sailboat design is vital: Consider various factors such as size, intended use, and sailing conditions when selecting a sailboat design. This will ensure you build a sailboat that meets your specific needs and provides optimal performance.
Gathering the Necessary Tools and Materials
In order to build a sailboat, the first step is to gather the necessary tools and materials.
- Start by researching the specific type of sailboat you want to build to determine the required tools and materials.
- Make a list of tools in good working condition, including a saw, hammer, drill, measuring tape, and screwdrivers.
- Create a material list that includes plywood, fiberglass, epoxy resin, screws, and nails . Calculate the quantities based on the sailboat plans.
- Find reliable suppliers and compare prices and quality for the materials.
- Set a budget for the project, taking into account the cost of both tools and materials.
- Plan the layout of your workspace for maximum efficiency and keep the tools and materials easily accessible and organized.
Throughout the building process, it is important to prioritize safety by wearing protective gear and following the guidelines for tool usage. If needed, seek assistance from experts or experienced builders. Building a sailboat may pose challenges but it is also a rewarding experience. So, enjoy the process and take satisfaction in creating something with your own hands.
What Tools Do You Need to Build a Sailboat?
To build a sailboat, you need the following tools:
1. Measuring tools: To accurately measure and mark dimensions, use a tape measure, ruler, and carpenter’s square.
2. Cutting tools: For cutting large pieces of wood, use a jigsaw or circular saw, and for intricate cuts, use a coping saw or handsaw.
3. Joinery tools: Assemble and join parts using a hammer, screwdriver, drills, and chisels.
4. Sanding tools: Smooth and shape wood surfaces using sandpaper or a power sander.
5. Clamping tools: Hold pieces together while working using clamps and a vise.
6. Safety equipment: Ensure your safety with gloves, safety glasses, and a dust mask.
In addition to these tools, you’ll need a well-ventilated workspace with a sturdy workbench. This is crucial for building a sailboat. It’s also advisable to have a set of plans or blueprints to guide you through the construction process.
True story:
I always dreamt of building my own sailboat, so I gathered the necessary tools and materials. With dedication and passion, I started constructing the hull, following the step-by-step process. It was challenging but rewarding. Installing the sails and rigging was exciting too. I could already envision the boat sailing on open water. After applying the finishing touches and conducting safety checks, it was time for the sailboat’s launch. With a mix of nerves and anticipation, I set the boat into the water. To my delight, it sailed smoothly, taking me on incredible adventures. Building a sailboat was a labor of love that fulfilled my lifelong dream of being a boat builder.
What Materials Are Required to Build a Sailboat?
Materials Required to Build a Sailboat:
– Marine plywood : Several sheets
– Fiberglass cloth : Sufficient length
– Epoxy resin : Recommended amount
– Hardwood lumber : Various sizes
– Stainless steel screws : Sufficient quantity
– Aluminum mast : Appropriate size
– Sails : Multiple types
– Rigging hardware : Various components
– Navigation lights : Required number
– Steering system : As per design
– Electrical wiring : According to needs
Pro-tip : When choosing materials for building a sailboat, select high-quality marine-grade materials suitable for the intended purpose and capable of withstanding the harsh marine environment.
Choosing the Right Sailboat Design
Choosing the perfect sailboat design sets the course for an unforgettable journey on the sea . Discover the key factors to consider in selecting the ideal sailboat design that suits your needs. Get ready to navigate through a sea of options and explore the world of sailboat aesthetics , performance , and practicality . So, prepare to steer your way into understanding the vital elements that influence the decision-making process when it comes to selecting the ultimate sailboat design .
Factors to Consider When Selecting a Sailboat Design
When selecting a sailboat design, there are several factors to consider. First and foremost is the intended use of the sailboat. You need to determine whether you plan to race , cruise , or day sail . It is important that the design aligns with your activities on the water.
Another crucial factor is the size of the sailboat. Consider your experience and crew when deciding on the sailboat size. Keep in mind that larger sailboats may require more crew members and expertise to handle.
It is essential to evaluate the stability of different sailboat designs. Factors such as keel type and hull shape can significantly impact the stability and seaworthiness of the sailboat.
Performance is another important consideration. Determine the level of performance you desire. Some designs prioritize speed and agility , while others focus on comfort and ease of handling .
Budget is also a significant factor to keep in mind. Take into account the price of owning and maintaining different sailboat designs, as well as ongoing expenses.
The construction material of the sailboat is yet another factor to consider. Options include fiberglass , wood , aluminum , and steel , each with its own advantages and considerations.
It is important to note that sailboats come in various designs, each with unique features catering to different sailing preferences and conditions.
Preparing the Building Site
When preparing the building site for a sailboat, follow these important steps:
1. Clear the area: Remove vegetation, debris, and obstructions to create a clean workspace.
2. Level the ground: Ensure the site is level and stable for a solid foundation.
3. Mark out the dimensions: Use measuring tools to accurately mark the sailboat’s length, width, and height on the ground.
4. Prepare the ground: Dig or fill the ground to create a smooth surface that meets the required dimensions.
5. Install boundary markers: Place stakes or markers around the perimeter of the building site to clearly define the boundaries and prevent encroachment.
6. Establish access points: Create pathways or access points to allow for easy movement of materials and equipment.
7. Ensure safety: Take necessary precautions such as putting up warning signs, setting up barriers, and having appropriate safety equipment on site.
By following these steps, you can effectively prepare the building site for constructing your sailboat.
What Are the Requirements for a Suitable Building Site?
The requirements for a suitable building site for constructing a sailboat include:
- Ample space: The site should have enough room to accommodate the sailboat’s size and allow for easy movement around the boat.
- Flat and level ground: The ground must be stable and even to prevent structural issues during construction.
- Protection from weather: The site should be sheltered from strong winds, rain, and direct sunlight to prevent material damage and ensure optimal working conditions.
- Access to utilities: Electricity and running water are necessary for powering tools, equipment, cleaning, and maintenance.
- Proper drainage: The site needs good drainage to prevent water accumulation, which can damage materials and hinder progress.
- Secure storage: A secure storage area is essential to protect tools, materials, and equipment from theft and damage.
- Accessibility: The site should be easily accessible for material delivery and transportation of the completed sailboat.
- Permits and regulations: Compliance with local building codes, permits, and regulations is necessary for safety and legal compliance throughout the construction process.
Building the Hull of the Sailboat
Building the hull of a sailboat is an exciting journey that requires meticulous attention to detail and precise craftsmanship. In this section, we will embark on a step-by-step process for constructing the sailboat hull, guiding you through the essential stages of this intricate endeavor. From selecting the right materials to shaping the structure, we’ll cover everything you need to know to create a sturdy and seaworthy foundation . So, grab your tools and let’s dive into the art of crafting the perfect sailboat hull.
Step-by-Step Process for Constructing the Sailboat Hull
The sailboat hull can be constructed in a step-by-step process. Here is how you can construct a strong and durable sailboat hull:
Step 1. Create the hull mold : Start by building a robust and long-lasting frame that accurately represents the shape and size of the hull.
Step 2. Prepare the mold surface: Apply a release agent to ensure that the hull does not stick to the mold.
Step 3. Lay fiberglass : Soak fiberglass cloth in epoxy resin and carefully place it on the mold, forming multiple layers to create a sturdy hull.
Step 4. Apply resin and cure: Distribute epoxy resin evenly across the entire surface in order to bond the layers together. Let it cure as per the instructions provided by the manufacturer.
Step 5. Sand and fair: Smooth out any imperfections on the hull, creating a sleek and flawless shape.
Step 6. Paint the hull: Enhance both appearance and protection by applying high-quality marine paint to the hull.
Step 7. Install hardware: Securely attach cleats, hatches, and fittings to prevent any leaks or damages.
By following these step-by-step instructions, you will be able to construct a sailboat hull that is strong, durable, and ready for the next stages of building your sailboat.
Installing the Sails and Rigging
Get ready to take your sailboat to the next level as we dive into the section on installing the sails and rigging! We’ll be revealing the secrets to properly attaching and rigging the sails for optimal performance. With expert insights and practical tips , you’ll soon be harnessing the wind like a pro. So, tighten your ropes and get ready to set sail on this exciting adventure of sailboat building!
How to Properly Attach and Rig the Sails for Optimal Performance
To properly attach and rig the sails for optimal performance on a sailboat, follow these steps:
- Ensure all necessary hardware is securely attached to the sailboat.
- Attach the halyard to the head of the sail and hoist it up the mast to the desired height.
- Secure the tack of the sail to the tack fitting at the bottom of the mast.
- Attach one end of the mainsheet to the boom and the other end to the traveler .
- Connect the jib sheets to the clew of the jib sail.
- Rig any additional sails according to manufacturer’s instructions.
- Check all lines and rigging for proper tension and alignment.
- Test the rigging and sails in different wind conditions for optimal performance.
- Regularly inspect and maintain the rigging and sails.
By following these steps, you can learn how to properly attach and rig the sails for optimal performance on your sailboat.
Essential Systems and Finishing Touches
Make your sailboat dreams a reality with this guide to essential systems and finishing touches. Discover the ins and outs of installing electrical and plumbing systems, ensuring your vessel is equipped with everything you need for a smooth sailing experience . Learn the art of applying finishes and sealants to protect your sailboat from the harsh marine environment. Get ready to set sail with confidence and style !
Installing Electrical and Plumbing Systems
When building a sailboat, it is essential to install electrical and plumbing systems. Here is a step-by-step process to guide you:
1. Plan the electrical and plumbing layout: Determine locations for electrical outlets, switches, and plumbing fixtures like sinks and toilets. Consider placement for batteries, freshwater tanks, and wastewater holding tanks.
2. Install electrical wiring: Start by installing the main electrical panel and run wires to various components and outlets. Use appropriate wiring sizes and ensure secure connections. Include safety features like circuit breakers and grounding.
3. Connect plumbing lines: Begin by installing freshwater supply lines and connecting them to the freshwater tank. Install plumbing fixtures like sinks and toilets, ensuring proper sealing and secure connections. Then, install the wastewater plumbing system, including drain lines and a holding tank.
4. Install electrical and plumbing components: This involves installing electrical outlets, switches, and lighting fixtures. Ensure proper wiring connections and test the electrical system for functionality. For plumbing, install faucets, showerheads, and toilets, ensuring proper water flow and drainage.
5. Test the systems: Once everything is installed, test the electrical and plumbing systems to ensure correct functioning. Check for leaks, proper water pressure, and operational lights and switches.
6. Make necessary adjustments: If any issues are found during testing, make the necessary adjustments and repairs to ensure optimal functioning of the systems.
7. Secure and protect the systems: Once everything is working correctly, secure and protect the electrical and plumbing systems by organizing wires and pipes, using appropriate insulation, and securing any loose components.
By following these steps, you can successfully install the electrical and plumbing systems in your sailboat, ensuring functionality and convenience on your sailing adventures.
Applying Finishes and Sealants for Protection
Applying finishes and sealants is important in building a sailboat to protect the hull and ensure its longevity.
Clean the hull: Make sure the hull is clean and free from debris or contaminants. Use a marine-friendly cleaner and rinse thoroughly.
Sand the hull: Lightly sand the hull using fine-grit sandpaper to create a smooth surface. This will help the finishes adhere better.
Choose the right finish: Select a high-quality marine-grade finish suitable for the hull material, such as varnish, paint, or gelcoat.
Apply the finish: Follow the manufacturer’s instructions. Apply thin, even coats using a brush or roller and allow proper drying time between coats.
Seal the hull: After applying finishes and sealants for protection, use a marine-grade sealant specifically designed for boat hulls to protect it from water penetration.
Apply multiple coats: Depending on the desired level of protection, it may be necessary to apply multiple coats of finish and sealant.
Inspect and maintain: Regularly inspect the finishes and sealants for signs of wear or damage. Touch up or reapply as needed to maintain optimal protection.
In history, boat builders recognized the importance of protecting the hulls from the sea’s harsh elements by applying finishes and sealants for protection. They used natural materials like tar, pitch, or wax to seal the wood and prevent waterlogging. Advancements in technology and materials have led to more durable finishes and sealants. Today, boat builders have access to marine-grade products designed to provide exceptional protection and enhance the longevity of sailboats. By applying finishes and sealants for protection with care and proper maintenance, sailors can ensure their sailboats remain in excellent condition for years of sailing adventures.
Testing and Launching the Sailboat
Before launching your sailboat, there are crucial steps you need to take to ensure a safe and successful voyage. In this section, we will dive into the necessary safety checks to conduct before setting sail. We will also provide valuable tips from seasoned sailors to ensure that your sailboat launch goes smoothly. So, buckle up and get ready to embark on your sailing adventure with confidence !
Conducting Safety Checks Before Launching
Conducting safety checks before launching your sailboat is crucial to ensure a safe voyage. To guarantee a smooth sailing experience, follow these steps:
1. Carefully inspect the hull of the sailboat for any damage or cracks. Be sure to check the seams and joints thoroughly.
2. Take the time to check the rigging , including the mast , shrouds , stays , and halyards , for signs of wear, fraying, or corrosion.
3. Hoist the sails and test them to ensure they are functioning properly. Make sure that all sail controls are in good condition and working as they should.
4. It is important to examine the electrical system of the sailboat. Check the battery and wiring for any signs of damage. Verify that all lights and instruments are functioning correctly.
5. Inspect the plumbing system , testing the freshwater system and searching for any leaks or clogs that may cause issues during your voyage.
6. Take the time to review all the necessary safety equipment . Ensure that everything is on board and in proper working order.
7. Confirm that all navigation aids , such as the compass , GPS , and any other navigation instruments, are functioning correctly.
8. It is crucial to verify the functioning of all communication devices . Take the time to test the radio or any other communication devices that you may have on board.
9. Inspect the fuel and engine carefully. Check the fuel level, oil levels, and overall engine condition. Test the engine to make sure it is running smoothly.
By conducting these necessary safety checks before launching your sailboat, you can minimize the risk of encountering any issues during your sailing experience.
Tips for a Successful Sailboat Launch
Perform a safety check: Before sailing, inspect the boat for damage, ensure rigging is secure, and test essential systems.
Check weather conditions: Choose a day with favorable weather for launching. Avoid high winds or rough seas.
Prepare a launch area: Clear a suitable pathway, remove obstacles, and ensure sufficient depth and space.
Use adequate support : Use sturdy boat trailers or launch ramps for stability during launch.
Properly position the boat: Center and balance the sailboat parallel to the water’s edge using dock lines or ropes.
Release the boat gradually: Release the boat steadily to prevent damage or injuries.
Monitor the boat’s movements: Check for leaks or instability and address issues immediately. Adjust sails and rigging if necessary.
Enjoy your sail: Follow boating safety guidelines and have a great time on the water.
A friend built a sailboat from scratch and successfully launched it by following these tips. The weather was perfect, and everything went smoothly. With the boat securely supported and positioned, they released it into the water, and it floated beautifully. They had a memorable experience sailing without any issues. By following these tips, they ensured a safe and enjoyable journey on their newly built sailboat.
Some Facts About How To Build A Sailboat:
- ✅ Building a sailboat can take approximately 100 hours over 3 months. (Source: Instructables)
- ✅ The cost of building a sailboat can amount to around $1,000. (Source: Instructables)
- ✅ The first step in building a sailboat involves cutting out the parts using boat building plans and plywood. (Source: Instructables)
- ✅ Assembling the hull of a sailboat involves stitching and gluing the panels together. (Source: Instructables)
- ✅ Fiberglassing the hull of a sailboat makes it waterproof and strong. (Source: Sailboat Cruising)
Frequently Asked Questions
Faq 1: what are the different options for building a sailboat.
There are three main options for building a sailboat. The first option is refurbishing an old boat, the second option is purchasing a hull with the deck moulding already fitted, and the third option is to build a boat from scratch.
FAQ 2: How long does it take to build a sailboat?
Building a sailboat takes approximately 100 hours over a span of 3 months.
FAQ 3: Can I learn the necessary skills for building a sailboat along the way?
Yes, you can learn the necessary skills for building a sailboat slowly and avoid making mistakes along the way.
FAQ 4: Should I hire a professional surveyor before refurbishing an old sailboat?
Yes, it is advisable to involve a professional surveyor before taking on the project of refurbishing an old sailboat.
FAQ 5: What materials are needed for building a sailboat?
The materials required for building a sailboat include oak plywood, epoxy resin, epoxy hardener, silica thickener, wood flour thickener, masking tape, Japanese pull-saw, table saw, router, sander, jigsaw, drill, wire cutter, C-clamps, mixing cups, fiberglass cloth, glue, screws, and fasteners.
FAQ 6: How much does it cost to build a sailboat?
The cost of building a sailboat is approximately $1,000, excluding any additional costs for customization or specific features.
About the author
Leave a Reply Cancel reply
Your email address will not be published. Required fields are marked *
Save my name, email, and website in this browser for the next time I comment.
Latest posts
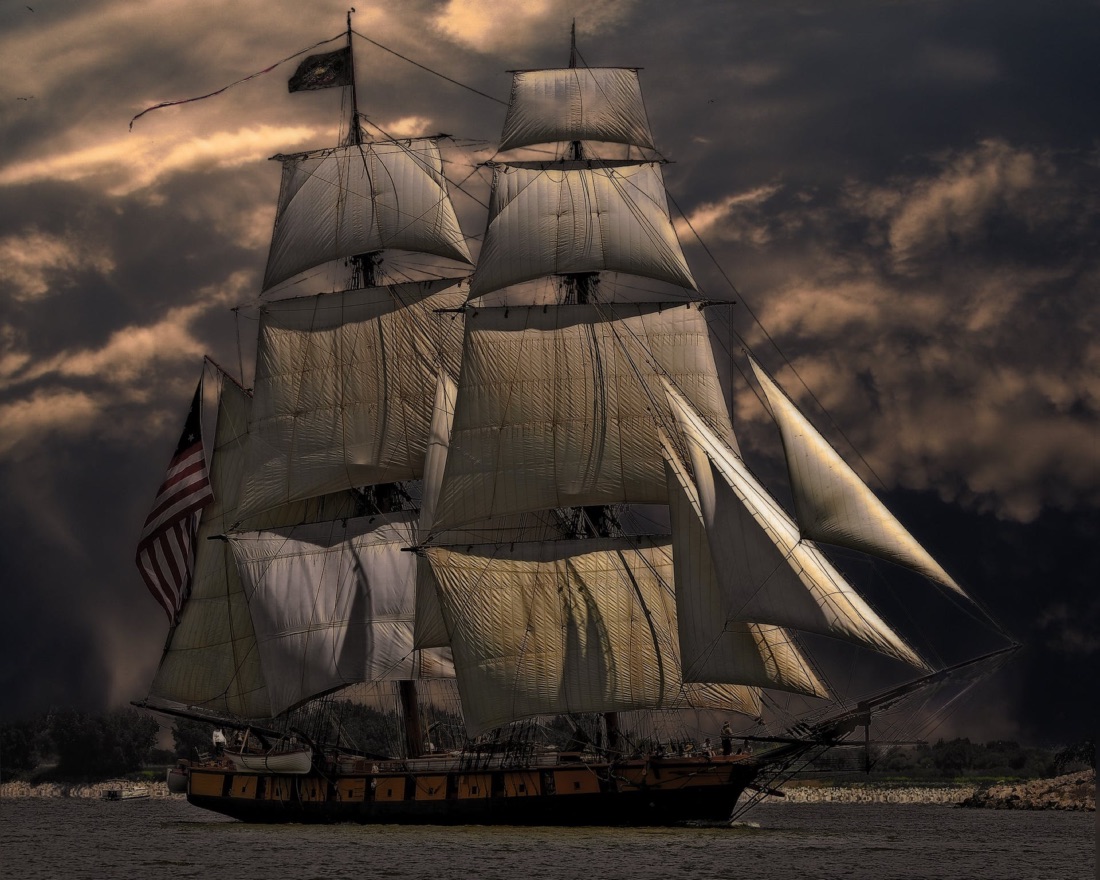
The history of sailing – from ancient times to modern adventures
History of Sailing Sailing is a time-honored tradition that has evolved over millennia, from its humble beginnings as a means of transportation to a beloved modern-day recreational activity. The history of sailing is a fascinating journey that spans cultures and centuries, rich in innovation and adventure. In this article, we’ll explore the remarkable evolution of…
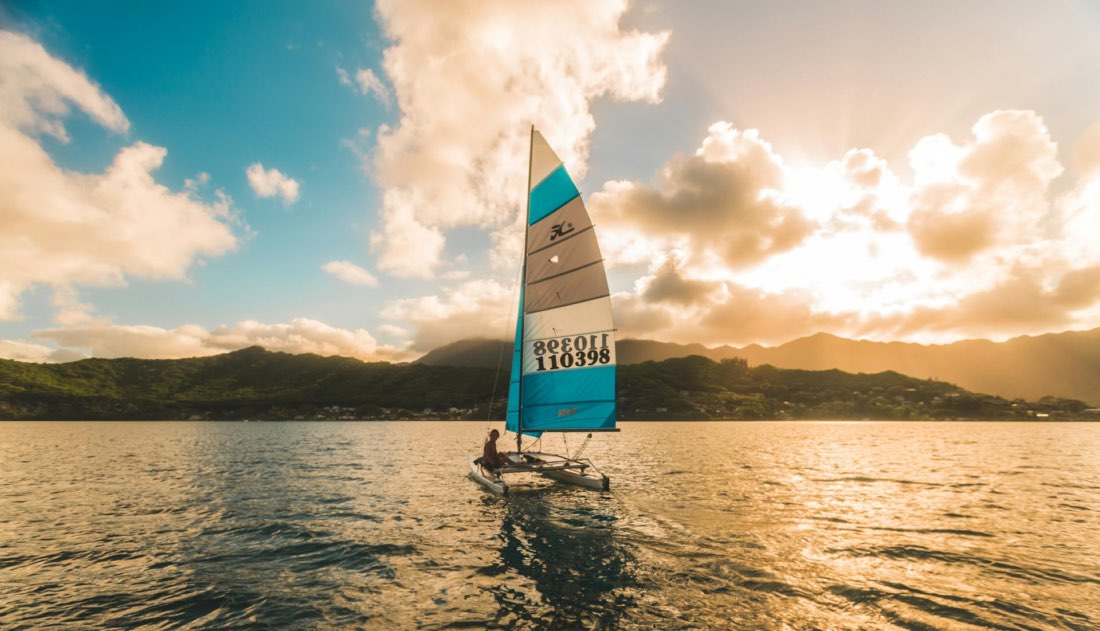
Sailing Solo: Adventures and Challenges of Single-Handed Sailing
Solo Sailing Sailing has always been a pursuit of freedom, adventure, and self-discovery. While sailing with a crew is a fantastic experience, there’s a unique allure to sailing solo – just you, the wind, and the open sea. Single-handed sailing, as it’s often called, is a journey of self-reliance, resilience, and the ultimate test of…
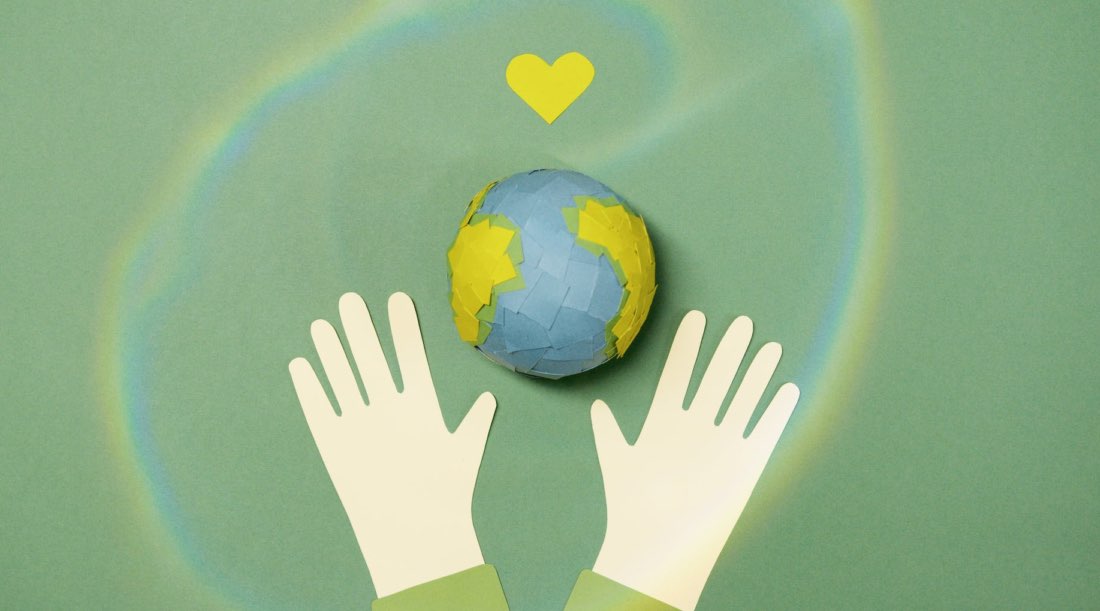
Sustainable Sailing: Eco-Friendly Practices on the boat
Eco Friendly Sailing Sailing is an exhilarating and timeless way to explore the beauty of the open water, but it’s important to remember that our oceans and environment need our protection. Sustainable sailing, which involves eco-friendly practices and mindful decision-making, allows sailors to enjoy their adventures while minimizing their impact on the environment. In this…
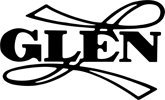
Boat Plans, Patterns and Supplies For the Amateur Boat Builder!
- Boat Plans Catalog – 300 Boats You Can Build!
- Boatbuilding Supplies & Epoxy
- Inboard Hardware
- Electrical Design Plans
- Books, DVD’s & Audio
- Boat Trailer Plans
- Raptor® Fastenings & Tools
- Glen-L RV Plans
- Gift Certificates
- Boatbuilder Blogs
- Boatbuilder Galleries
- Newsletter Archives
- Customer Photos Archives
- Where Do I Start…
- About Our Plans & Kits
- Boatbuilder Forum
- Boatbuilder Gatherings
- Boatbuilding Methods
- Featured Design on TV’s NCIS
- Our Boats in Action
Boatbuilding with Plywood
For most amateurs, plywood is the material of choice. Plywood is one of the cheapest and easiest building materials, one that the average do-it-yourselfer is both familiar and comfortable with. Plywood is also, pound for pound, stronger than steel. Because of its high strength to weight, plywood construction yields a boat that is much lighter and performs better than a “chopper gun” fiberglass boat. When used with the GLEN-L Epoxy Encapsulation System, plywood is as long lasting and as low in maintenance as any other material. No exotic tools are required, and with the possible exception of enough C-clamps, plywood boats can be built with the tools in the average home workshop. Plywood boats are frequently built in school wood shops or by youth groups as individual or group projects. To take full advantage of the material, our Plans and Patterns detail simplified construction methods geared to the abilities of the amateur. No difficult woodworking procedures, such as steam bending, are ever required, and the GLEN-L pattern system makes the difficult lofting procedure unnecessary.
Plywood is used as a “sheet” material in the majority of plywood boats, including Stitch-N-Glue. Plywood is also used in “cold-molded” construction and “multi-diagonal” planking. On each design page the method is listed under “Hull” in Characteristics.
SHEET PLYWOOD: This is the most common type of construction used by the home builder. Plywood is used in panels of one or two layers. This requires a minimum of cutting and fitting and requires much fewer frames than most “traditional” planking methods. For a look at the steps in plywood boatbuilding in more detail see our Sheet Plywood Pictorial Guide with captions .
COLD-MOLDED or MULTI-DIAGONAL: This method is utilized on round bilge hulls or hulls with compound shapes. The method involves cutting the plywood into strips (widths vary depending on curve), and laying up layers at angles to each other, glued and fastened. Epoxy is the recommended adhesive. Multi-diagonal Planking Pictorial Guide.
Uncommon Answers to Some Common Questions by Ken Hankinson, Naval Architect:
C ertain questions about plywood and its use in boatbuilding crop up time and again. Usually these are based on a desire to get the most value for the least bucks, to save time and effort, and to assure a level of quality that’s acceptable to the builder. Note that I didn’t say that builders ALL want ultimate top quality, and that’s intended. Just as in production boats, top quality is not always demanded, needed, nor expected. After all, not all boats need to last so long that they become exhibits in museums.
Q: Must all plywood used for boatbuilding be waterproof?
A: Basically there are three plywood grades; Interior, Exterior, and Marine. The typical assumption is that plywood used in boats must be made with waterproof glue. However, the accepted standard for such a glue is one whose bonds will survive a boil test. How many boats are ever subjected to boiling water conditions? None I know of.
Fact is, for generations, countless plywood boats have been glued together successfully with low-cost powder-water mix plastic resin glue (a urea-formaldehyde product). And while highly water-resistant, this glue won’t survive a boil test and is thus not considered totally waterproof. But it will survive hundreds of consecutive cycles of immersion in water at room temperatures.
The point is, Interior grade plywood is not rated for exterior or marine use where such panels may be exposed to moisture because grading standards permit non-waterproof glues in their manufacture. However, does this mean that such a panel might fail if exposed to exterior or marine conditions? Perhaps not if it is assembled with a highly water-resistant glue such as plastic resin. But one won’t know if such a glue has been used. Thus I ordinarily advise NEVER to use Interior plywood in a boat strictly because the standards permit use of a non-waterproof glue. Besides, the practice is penny-wise and pound-foolish. For structural members, stick to either Exterior or Marine panels.
Q: When should I use Marine plywood?
A: Some feel ONLY Marine plywood should be used for hull planking. But I think this is too rigid a rule. The important quality separating Marine grade from Exterior panels is the quality and soundness of the inner plies and their construction (both are made with waterproof glues as noted above). With the Marine panel, there should be no major voids or surface defects, and inner veneer joints (if they occur) should be tightly fitted.
That said, using Marine plywood is most critical in my opinion where panels must conform to rather extreme curvatures (the bow in most boats, especially the bottom), and for boats built with “stitch-and-glue” methods. Another case where Marine plywood would be highly advised is on boats intended for high speeds and/or severe service.
Here’s some reasoning. You might be able to save some bucks by using Exterior plywood for planking curved areas. And experience tells me that once such a panel has been bent into place, if it doesn’t fracture in the process, it will probably stay that way forever without incidence.
But the problem with lower-quality panels is that you may not always see the voids. And if your panel does break while you are installing it due to hidden voids, you will have to replace it with another, thus making the cost about comparable to what you would have spent on the better Marine panel in the first place. And there’s no guarantee that the next panel won’t fail as well.
As for “stitch-and-glue” construction, a void-free panel for planking is important so that the wire ties at joints don’t pull out under tension, which is likely to occur if stitching holes need to be located coincidentally with a void that suddenly crops up once the panel has been cut to shape. Such panels are also easier to work with for the same reasons when used for internal members and bulkheads on “stitch-and-glue” boats.
Q: When can I get by with Exterior plywood?
A: Other than as stated above, I’m not against using a good grade of Exterior plywood (for example, AB) for planking, and I’ve never heard of a boat falling apart because of it. You may have to make some repairs to the panel (e.g., fill voids) which can get tedious and is not always successful. But in flatter hull areas such panels will suffice for most boats. Exterior panels (with any major defects repaired when possible) can usually also be used for most internal members throughout a boat without problem for such items as transoms, gussets, bulkheads, etc.
In fact, I’m not totally against using lesser-quality AC plywood for planking on certain boats. In case you don’t know, an AC panel can have open and exposed defects on the C-side. But since the boat will probably by sheathed with fiberglass, some builders use the C-side outside and fill all the defects with resin putty prior to fiberglass application; they become invisible once painted. On smaller, simpler, low-powered boats without a lot of curvature, I see nothing wrong with this practice, and again, have not heard of such a boat disintegrating over time because of it.
Q: Why should I cover my plywood boat with fiberglass?
A: We generally recommend covering all plywood boats with fiberglass no matter how small. While some complain of an increase in weight, this is seldom more than an ounce or two per square foot of area in the typical application. Then too, even lightweight coverings (say 4 ounce cloth) are better than nothing.
When I speak of covering the outside of plywood boats with fiberglass, I use the term generically; you can use other fabrics such a Dynel or polypropylene, but fiberglass gives the best combination of price, ease of application, ready-availability, and protection in my opinion. Whichever fabric you select, the reasons for applying the covering are the same; added abrasion resistance, improved durability, extra reinforcing for finish coatings (especially at joints), reduced maintenance, better appearance, and to help insure against leaks.
Thus sheathings should be considered as basically cosmetic coverings; their intent is NOT to add strength. In fact, plywood is far stiffer than fiberglass. Hull strength comes from the plywood hull structure itself, and with proper design and construction, should prove more than adequate.
Glen-L carries epoxy , fiberglass cloth and application materials .
Q: What happens if I don’t sheathe my plywood boat with fiberglass?
A: If it is made with Douglas fir ( a reasonably tough material), surface checking and wavy surfaces will soon occur even if painted. These will be very difficult to alleviate even if the boat gets painted each season. Other plywood types with a more uniform grain pattern will fare better in this regard, but these will still require routine coating applications. And because many species of plywood are not as tough as fir, they will more easily suffer damage without sheathing.
If you absolutely insist on not sheathing your plywood boat, consider using medium-density overlay (MDO) panels. These still require routine coating, but the overlay prevents surface checking and presents a smooth paint-ready surface. These do cost more and may not be readily available, however.
Q: Epoxy resins sound great but they cost too much. Can I use polyesters for sheathings instead?
A: We quit offering polyester resins for sheathing application years ago simply because we no longer believed in them anymore for this purpose. Our feeling is that as long as you’re going to the trouble, you should use epoxy resins if at all possible; they’re worth the extra cost. The main reason is that they stick forever, and if you’re using as epoxy encapsulation system, (also highly advised), they are the only choice.
That said, if you are on a budget, polyesters are acceptable if you do it right, but they don’t have true adhesive properties. Finish results with either otherwise appear the same, but polyesters are less flexible and resilient so tend to crack more easily over time. When this occurs, water can creep behind the sheathing and cause problems.
As for the encapsulation process where all wood surfaces inside and out get coated, do NOT substitute polyesters this way in place of epoxies. Polyester resins simply don’t work the same; they don’t stick or apply well, and because of their lack of elasticity, crack easily which can promote rot due to entrapped moisture.
See the epoxies available from Glen-L.
Q: Epoxy glues may be superior but I’m allergic to them – what’s next best for plywood boatbuilding?
A: Because the stresses on a plywood boat are ultimately transferred to joints in the hull, a hard-setting glue (rather than a flexible mastic, for example) is required. As a result, glue choices are few. Prior to epoxies, the traditional stand-by’s were plastic resin and resorcinol. The latter is 100% waterproof while plastic resin is considered “highly water-resistant”. But as discussed above, plastic resin glues can work successfully in plywood boats for all practical purposes.
Currently resorcinol costs more than epoxies, and offers no benefits over plastic resin glue in my opinion. Unlike epoxies, both need well-fitted joints, specific limited temperatures, heavy clamping pressure, and leave colored glue lines. Since plastic resin glues don’t stain and clean up easily, mix with water, and are a fraction of the cost of resorcinol, they’re my choice in lieu of epoxies.
The only other alternative I’m aware of and have used with good results in the past is Aerolite, a water-resistant urea-formaldehyde based product by Ciba-Geigy sometimes imported from England but seldom found. This uses a powder-water mix along with a second liquid component, dries clear, and has some gap-filling properties. Once popular with kit airplane builders, it may still be available from suppliers in that field.
Glen-L’s Poxy Grip is an excellent adhesive for your Glen-L boat.
Q: Can I increase fiberglass thickness in order to get by with thinner plywood or compensate for lower quality plywood?
A: I don’t know how this line of thinking evolved, but the question keeps coming up. Primarily it involves the fallacy that plywood is weaker than, and inferior to, fiberglass. Keep in mind that while fiberglass is strong in tensile strength, it is not very stiff. Conversely, plywood is actually stronger on a weight basis in both tension and compression. More to the point, the modulus of elasticity (stiffness) is actually much higher for plywood than fiberglass for the same thickness.
Then too, for some reason many who ask this question think fiberglass is lighter and will thus save weight. This myth is quickly dispelled when a piece of each material gets thrown into a pond of water and the fiberglass sinks like a stone while the plywood floats.
So the simple answer is that if you reduce plywood thickness and make up the difference with fiberglass laminate, you get not only a more flexible panel, but one that weighs a lot more. It will also add considerably to your cost and effort. And if this question is asked because thicker panels are not available, the answer is to use a double thickness of plywood rather than attempt to make up the difference with fiberglass.
Q: Why is Marine plywood so expensive?
A: As for domestic panels, my first reaction to this question is that we’re fortunate to have any Marine plywood available regardless of the price. Of the total amount of plywood produced in this country, less than 1/10 of 1 percent is Marine grade. Environmental and economic factors, coupled with very modest demand should warrant even higher prices in the eyes of producers. And if you consider the price of plywood compared to other materials, it’s actually a bargain. On a cost per square foot basis, many common materials are considerably more expensive than plywood, such as carpet and resilient floor coverings. And you can’t even build a boat from that stuff.
While imported Marine plywood panels might cost twice as much as the domestic product or more (and we’re again fortunate to have this competition available regardless of the price), this is still a reasonable price compared to other alternatives.
Compared to all the other boatbuilding materials an amateur may use, only steel is cheaper than sheet plywood. And when you consider the speed and ease with which a plywood boat can be built, it’s still the material of choice for most do-it-yourself builders.
Q: Can I make frames out of plywood rather than solid lumber?
A: This is generally poor practice in the framed plywood boat for several reasons. First, a main reason for using solid lumber for frames is that grain gets oriented in the direction we want for strength. If plywood is used for frame members instead, because of the alternating grain direction of the plies, there is no strength in those veneers in the cross-grain direction. In other words, a plywood frame will need to be nearly double the thickness to have the same strength (see Fig. 1 below).
Second, longitudinal strength members (e.g., keels, chine logs, sheer clamps, stiffening battens, etc.) that intersect frames will require fastenings at contact points. If the frames are plywood, the edge grain of frames at such intersections will hold fastenings poorly, and if other than Marine panels are used, there is a possibility of voids at a point where they are least desirable.
Third, attempting to bevel or fair such frames when necessary is difficult because of the alternating grain pattern at edges. The tendency is to splinter the frame edges instead.
On the other hand, using plywood for joining sawn frame members via gussets, floor timbers, and the like is excellent because the alternating grain at such connections reduces splitting that would occur if solid wood members were used (see Fig. 2 below).
FIG 1 – Because of plywood’s cross grain, a plywood frame will be flimsy and not as strong as one from lumber of the same thickness. FIG 2 – However, because of plywood’s cross grain, using gussets, floor timbers, and similar members to join sawn wood frame members will largely prevent splitting at such connections.
Q: If frames shouldn’t be made from plywood, what about stems?
A: Actually stems from plywood, as long as they are thick enough (1-1/2″ is a nominal minimum) are preferable to solid lumber on the plywood boat. The reason is that a plywood stem is more dimensionally stable due to the cross grain. Such reduction in expansion and contraction reduces any tendency for movement or cracking along the centerline where planking halves join. While it could be argued that the plywood stem presents edge grain for the planking fastenings, in reality the bevels required here allow fastenings to set diagonally to the grain for a solid grip if long enough (see Fig. 3A) . An acceptable alternative is the stem made with a core of plywood and solid wood on both sides (see Fig. 3B) .
FIG 3 – A section through a plywood stem (A) shows that because of the bevels required, fastening into edge grain is largely avoided. An alternative is a stem with a plywood core and solid wood either side (B).
Q: Why shouldn’t sheet plywood planking be fastened to transverse frames?
A: The properly designed plywood planked hull incorporates as much as possible the principles of monocoque or “stress-skin” construction. Stitch-and-glue boats that depend upon glue bonded junctions reinforced with fiberglass tape often show pure adherence to such principles. However, not everyone is willing to trust their fate only to glue bonds; many still favor the extra security that fastenings and some internal framework can provide. After all, such construction has been proven strong and durable for generations whereas stitch-and-glue is still the new kid on the block.
But even when transverse frames are part of the design, it’s the plywood skin that takes the stresses which are ultimately transferred to glued and/or fastened joints at panel edges. And if such panels are fastened across the grain to frames, localized stresses that can lead to failure of the panel can be generated. How so?
Consider a plywood panel curved in place around a hull as being analogous to corrugated cardboard applied in similar fashion with the corrugations running lengthwise. We can pin or tack such a cardboard panel in place all around the edges to hold it in place. But what happens to the cardboard if we perforate it with a bunch of fastening holes crosswise? When bent in place, it would fold and break about the perforations.
The same thing can happen in a sheet of plywood. Placing a row of fastenings across the plywood panels grain can weaken a panel and create a similar condition, especially so when the panel is also under tension due to bending. Conditions are exacerbated on the higher-speed powerboat where panel loads are greatly magnified due to slamming loads while planing.
In short, while frames on the plywood boat may contact planking and be glued at such points, ordinarily such contact is not actually necessary and in fact, frames can usually be relieved from such contact without detriment. In reality, it’s the longitudinal members doing most of the work and this is why planking panels are preferably fastened only to these and at the ends of panels and NOT to frames between.
Q: What about using plywood for sailboat rudders, centerboards, and daggerboards?
A: If a Marine grade panel is used, and these are thick enough (say 1″ or more), plywood is sometimes acceptable. However, I’ve seen many plywood rudders and daggerboards break in use, and again, the problem is that areas of cross grain within a panel tend to be weak and lead to fracture. Sailors often don’t realize just how much stress can be applied to a rudder turned hard over on the small sailboat or just how much force a capsized sailor exerts while standing on a daggerboard attempting to right the small dinghy.
Another difficulty is that rudders and daggerboards should be faired to an airfoil sectional shape which is not as easy to do with plywood. Thus solid wood is preferable, or you might use a rudder or daggerboard with a plywood core (1/2″ or thicker with solid lumber laminated to both sides (see Fig. 4A and 4B) . Plywood boards and rudders should be encapsulated with epoxy and fiberglass cloth in any case.
FIG 4 – A section through a sailboat rudder faired to an airfoil below water (A) is difficult to do with plywood; solid wood is preferable. However, one with a plywood core and solid wood each side is acceptable and perhaps preferable for larger rudders where solid wood will tend to split and/or must be glued up from narrower widths (B).
Q: Can I use nails in place of screws for fastening plywood planking and decking?
A: As a general rule on the framed plywood boat, because planking panels carry loads to the panel edges, screws give superior holding ability compared to nails, especially when panels are under the stress of bending. Nails in this situation lack the leverage inherent in screws to maintain this tension if a glue joint lets go for some reason (albeit a rare occurrence).
Conversely, in flatter areas of a hull (especially on small boats or those not intended for high speed or rough water use), and at mid areas within a panel, nails are acceptable if long enough and of ample wire size. In most cases, deck panels can be nailed although I still prefer screws at panel edges in the case of powerboats since the deck is usually an important strength membrane.
While nails may be relatively inexpensive, you should still pre-drill pilot holes for all but the smallest sizes. As for driving screws, do NOT countersink the heads below the outer veneers of the sheet of plywood; the screw should compress all veneers in the panel (see Fig. 5A and 5B) .
FIG 5 – The “right” way (A) and “wrong” way (B) to drive a screw used to fasten plywood planking. All veneers in the panel should be under compression.
Glen-L carries silicon bronze nails and screws as well as stainless steel fastenings for above the waterline.
Comments are closed.
Connect with us:
Customer builds.
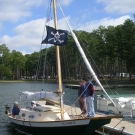
Useful Information
- Cost & Time To Build
- Links & Suppliers
- Online Glossary
- Support Knowledge Base
- Teleseminars
- Wood & Plywood
Building Links
- How Fast Does It Go?
- Install A Jet Ski Motor
- Modifying The Motorwell
- Sailboat Hardware Notes
Glen L Marine Design
- About Glen L
- How To Place an Order
- Privacy Policy
Copyright Info.
Copyright 2006-2022 by Glen L Marine Designs. All rights reserved.
Mailing Address: 826 East Park Ave. Port Townsend, WA 98368
Web design by Big Guns Marketing , LLC.
One Sheet Plywood Boat

Introduction: One Sheet Plywood Boat
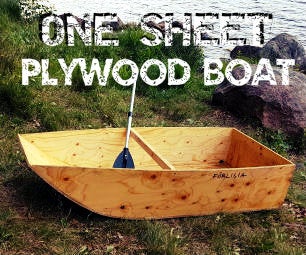
I have always wanted to build myself a boat. This was maybe not the one I had in mind. But I have to start somewhere I guess.:-)
It's a pretty simple and quick build. The boat is made from just one sheet of cheap construction plywood.
I made a little video of the build if you want to see the process in moving pictures too.
Video of the one sheet plywood boat
- circular saw
- jig saw (optional)
- drill (with a drill and countersink bit)
- impact screw driver
- long ruler/straight edge
- Sanding block
- Pen and tape meassure
Other things used
- Silicone (wetroom FA180)
- Screws (drywall screws)
- Linseed oil for protection of the wood
Step 1: Meassuring and Marking
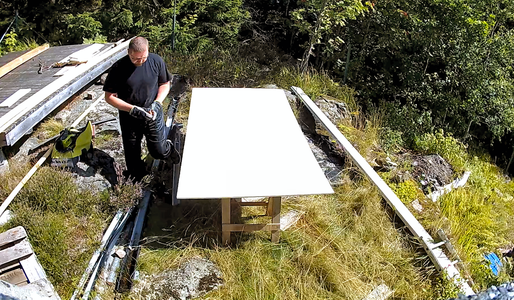
Here is my layout of the sheet.
I made my boat a bit shorther than it needed to be. I cut off about 40 cm (the top of the sheet in the second picture). Why? Several reasons. :-)
- I wanted it to fit inside our car
- I wanted it to be easy to carry
- I was unsure if I needed to reinforce any part, so I needed to save some plywood for later.
Step 2: Cutting the Parts
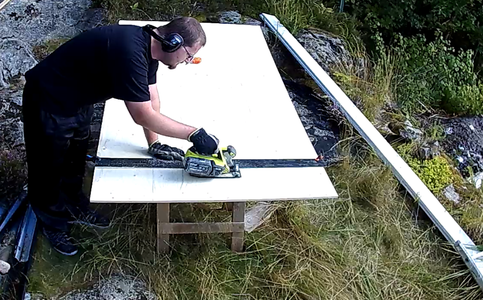
I used a circular saw to cut the parts.
The boat will be constructed out of four parts in total. A bottom and three sides.
Step 3: Bending the Boat
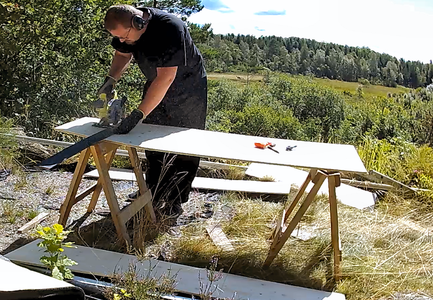
I have seen other design where the bottom is cut to make a angle in the front of the boat. I wanted to have a bent bottom instead.
As you see in the pictures (hopefully) this is when the sides gets it final length and angle (in the for). I hold one site up to the bottom and trace the curve. the I use that side as a template to trace on the other piece to make them the same size. If you cannot hold the pieces by hand, use some clamps.
The thickness of this plywood is 1,2 cm. I set the depth on my circular saw to 5 mm and cut lines where I wanted to bend the plywood.
I will later put silicone in the cut-lines so the structure will be rigid.
When I can see that the plywood bottom bends right, I hand sand the parts before putting it all together.
Step 4: Parts
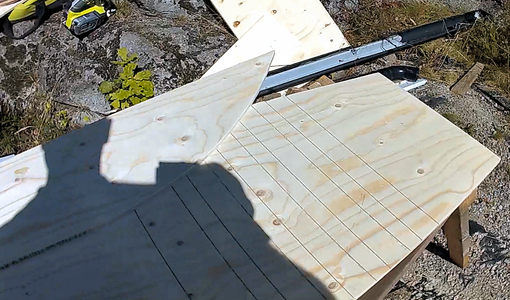
Here is the parts. You can also se the lines in the front of the bottom that makes the plywood being able to bend.
Step 5: The Assembly
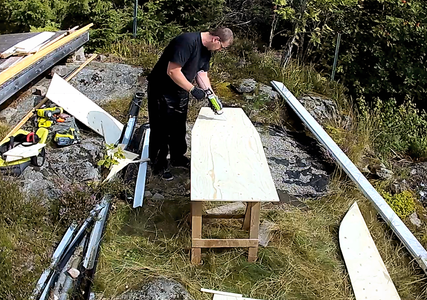
I put silicone around the bottom and use a small nail gun, just for speeding the process up. I use as few nails as I can. Then I put the left side on, the back and then the right side.
I put a few screws in for support.
Remember to pre-drill and counter sink all the screw holes.
I actually put silicone in each screw hole and on top of every screw too.
Step 6: The Bottom
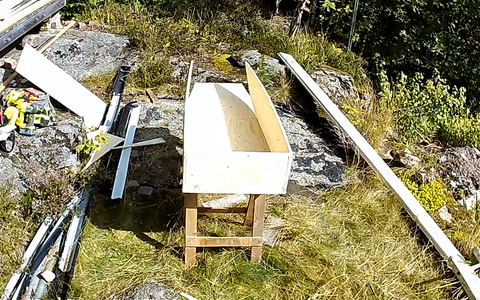
When the sides is mounted, and bend the front to the sides and put in screws. Then I add more screws from the bottom side.
Remeber to seal everything with silicone.
Step 7: The Result
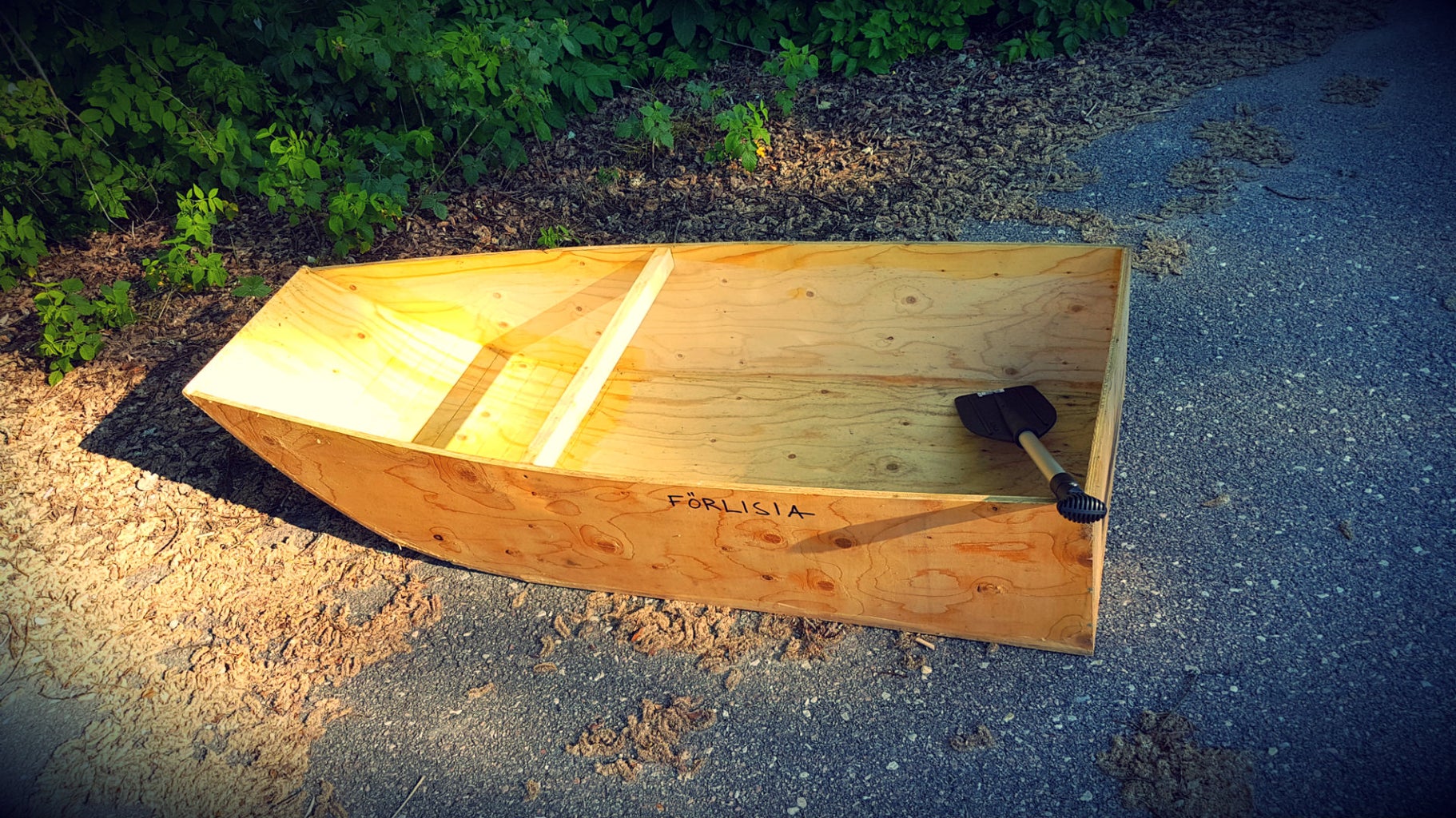
There is some more pictures of the boat "Förlisia" and action shots is found in the video here . :-)
This was a really fun build and a perfect summer project. Took a couple of hours to make. I had no plans to go on, so I made things up as I went along. So I have some suggestions for improvement.
Improvements
If possibe - use the entire length of the ply sheet.
If you are not as heavy as me, you can have shorter sides (making the bottom wider and the boat more stable in the water). I had 30 cm height on the sides. If you go with 25 cm instead, you get 70 cm wide bottom instead.
I would place some runners underneath the bottom, making the boat go more straight in the water.
I would make something to sit on, so its more comfortable.
Thank you for reading this instructable! Please let me know if you have any questions or let me know what you think. It's much appreciated! You can also look at my other projects here on instructable or check out my YouTube channel.
A vote for the boat?
I entered the Water Contest , so if you like this project please consider a vote for this little boat! :-) It would be much appreciated! Thanks again!
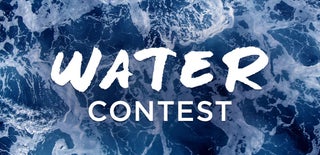
Runner Up in the Water Contest
Recommendations
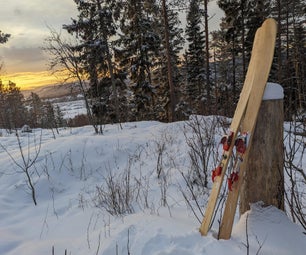
Remake It - Autodesk Design & Make - Student Contest
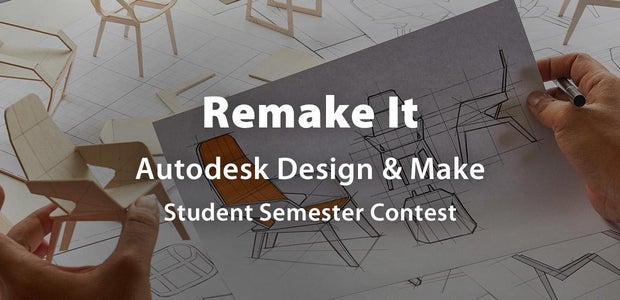
Green Future Student Design Challenge
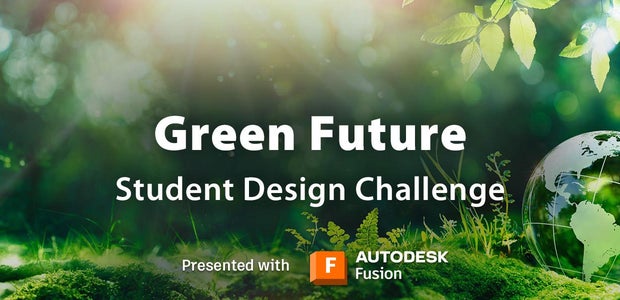
All Things Pi Contest
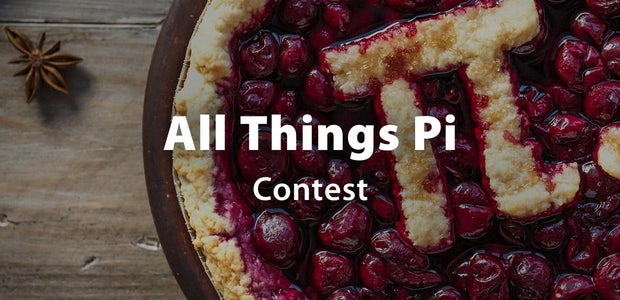
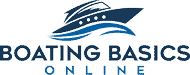
Boating Basics Online is reader-supported. When you buy via our links, we may earn a commission at no cost to you. Learn more
How to Build a Plywood Boat in Easy and Simple Steps
Written by J. Harvey / Fact checked by S. Numbers
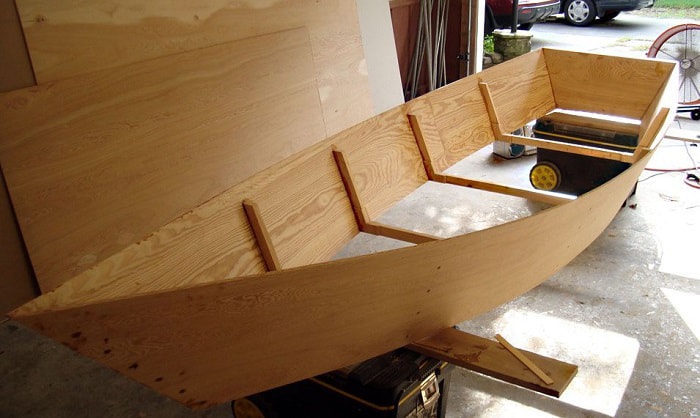
There’s always a different sense of satisfaction using something you built with your own hands. Instead of going to a professional plywood boat builder, building a plywood boat yourself and using it will bring a different sense of satisfaction.
In this short guide, we’ll go over the steps on how to build a plywood boat yourself. It’s a worthwhile and valuable experience that any boating enthusiast should experience for themselves. Read on to learn more.
Table of Contents

What You’ll Need
1. determine the kind of boat you want, 2. procure a boat building plan, 3. choose and prepare materials, 4. build the boat according to the building plans, 5. apply epoxy resin, 6. lay the fiberglass cloth, 7. wet out the fiberglass cloth, 8. coat with primer, 9. apply boat paint, 10. apply boat polish and wax, 1. use marine-grade materials, 2. sand every surface, 3. use power tools for more efficiency.

- Marine plywood and wood pieces (as indicated by your boat plan)
- Marine glue
- Epoxy resin
- Fiberglass cloth
- Sandpaper and orbital sander
- Paintbrushes
- Painter’s tape
- Saw for wood
- Polish and wax
- Hand polisher
- Fiberglass cloth roll
Steps to Build a Plywood Boat
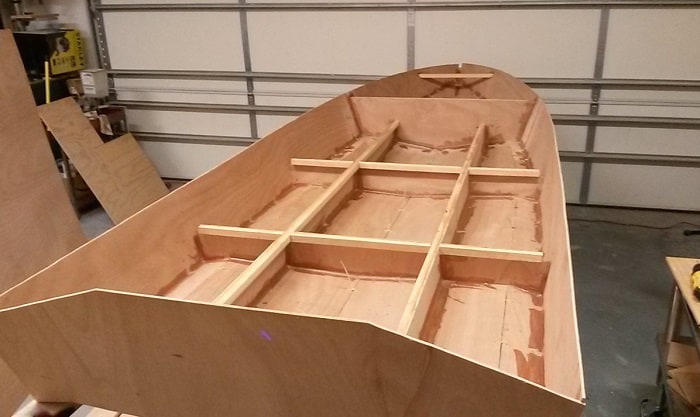
The first step is to plan your boat-building project. Determining the kind of boat you want, such as a plywood fishing boat, will make it much easier to plan everything else. Decide on what body of water you’ll want your boat to traverse, its size, and what you want to have on board.
For your first build, it may be better to consider something that’s not too big, at least until you’re confident enough about your building skills. Just be sure to plan ahead for whatever you can. Don’t stress about covering everything, just plan what you can and things will be easier down the road.
After you’ve determined which boat you want to build, it’s time to procure the materials you’ll be using. For boat building, it’s recommended not to skimp on material quality. But there is one item you should get first.
The first crucial item you’ll need is a boat plan. There are free plans available, but it will be better for you and your project to go with plans from a reputable source. Premium boat plans will detail how to build a wooden boat step by step and are easier to read compared to free plans that could even be outdated.
On top of the list is your plywood, and marine plywood is recommended. For certain parts of the boat such as the hull, marine plywood makes sense. However, it’s a good idea to use marine plywood for the entire boat to save yourself a lot of work and worry.
Marine plywood will make the work easier because you won’t have to cover as much area with resin as marine plywood would have almost no voids. You may even end up spending more if the project ends up requiring more resin than you planned for.
Next up, build the boat itself based on the boat plans you procured. If this is your first build, try to stick to the plans as closely as possible. Even small deviations may have implications that you may not be capable of predicting.
Detailed boat plans should also have the necessary amount of materials you’ll need along with measurements for the wood, among other things. Try to review the plans before proceeding with assembly and adjust your plans accordingly.
Apply epoxy resin over the entire boat surface. The important thing about applying epoxy resin is to create an entirely smooth surface. If there are any gaps or voids on the wood surface, you will have to fill those in with the resin.
Don’t be afraid to use too much epoxy on voids that have bumps. Gaps are what we absolutely want to avoid. Sand down the surface to smooth everything out. Try to be thorough since imperfections will be noticeable after the project.
Let the resin dry before proceeding to the next step.
Cut the cloth to size and let it relax for a few days before working to ensure that the surface is smooth once finished. After the cloth has relaxed, smooth the surface of the cloth to iron out any wrinkles or creases. You can use your hand or a tool to do the smoothing.
You can use some tape to hold the cloth in place as you smooth it; do this a few times until the cloth is free from wrinkles. This is important to keep the finish consistent. Let the smoothed cloth rest overnight before proceeding to wet the surface.
Before wetting the fiberglass cloth, give it another run to make sure that the entire surface is level. Use a thin layer of epoxy resin to wet the surface of the cloth. Make sure that the surface is smooth before it dries.
You’ll know that the cloth is applied properly if it becomes transparent and sticks to the boat surface quickly. You can use a roller to even out the surface, but do this while the resin is still wet.
The next step is to paint the boat with fiberglass paint. Applying primer first, around two to three coats should do the trick. Make sure that you apply the primer carefully; a consistent coat is very important for a beautiful finish.
Work in sections so you’ll have enough time to work with the primer. After finishing the first primer coat, let it dry before applying the next coat. After the primer coats, apply your paint of choice and as with the primer, work in smaller sections to make the working time of the paint manageable.
Apply the paint horizontally using a brush, then go over the painted area with a brush but vertically. This will produce a smooth painted surface, but the key is to be quick about the second brush, which is why working in sections makes great sense.
Paint the whole surface of the boat with emphasis on making the coat as even as you can. I prefer using semi-gloss paint because its finish is hard.
The final step is to apply polish and wax to the boat’s surface. This will give it that shiny finish that will make your boat look good and also protect it against harsh marine conditions. Try to stick to the instructions provided by your chosen product.
Some products combine polish and wax in one product, and those should be fine to use as well. Just make sure that you do a thorough application of the product to make your boat extra shiny.
Now you’re done. All that’s left is to set out on your own DIY plywood boat.
Read more : Steps to build a fiberglass boat.
The use of marine-grade materials is recommended to save yourself trouble later on. Since the entire boat is covered in resin, water-proofing is not the biggest benefit of marine-grade materials but they’re there for a sense of security.
It’s said that it’s better to err on the side of caution, and as safety should always be a priority for boating, I think it’s good to consider the use of marine-grade materials if only for safety considerations.
The key to a beautiful boat finish is a smooth and consistent surface. Any gaps or breaks on the boat’s surface are a blemish on what could have been an excellent piece of workmanship. Sanding helps ensure a consistent and smooth finish.
To produce that consistent finish, it is necessary to sand down in between steps. Before and after applying resin on the boat, after each primer coat, and after applying each coat of paint, sanding needs to be done for all of these.
While it may take a lot of work, the result will be the best look you can achieve.
While using tools such as an orbital sander or a motorized polisher is not required, they make the work more efficient. Using tools makes the work much easier, which can help bring about an even better result.
Making a homemade plywood boat is time-consuming. Consider using tools, especially if you want to save time.
And that’s how to build a plywood boat. While it may take some time to complete, it’s simpler than many people would think. Hopefully, it will be fulfilling and rewarding to you.
I certainly hope this short guide was helpful to you. Please share it with other people who might find it useful as well. Leave your comments below. We’d love to hear about your thoughts and experiences with your own plywood boat construction project.
Remember to boat safely.
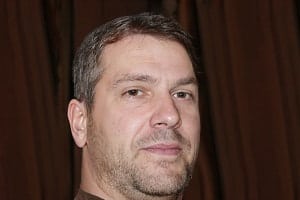
“My intention from the first day establishing Boating Basics Online is to provide as much help as possible for boaters who want to experience a first safe and convenient trip. So feel free to join us and share your beautiful journeys to the sea!”

- About Modern Wooden Boats
- Tips & tricks
- What’s inside a boat plan ?

Idea 21 sportboat
The development of the family of small offshore capable sailboat plans : chined hull for the highest stability, vertical lifting keel, trailerable, suitable for club racing or cruising (two interior versions) , plywood and epoxy hull with the radius chine system, sparkling performances while sailing and reasonable interiors for coastal cruising.
First boat launched : read the first impressions here
Idea 21 small sailboat plan is the latest development of my family of small plywood & epoxy sailboats plans for homebuilders : it was quite a time since i was thinking of an evolution of her smaller 19 footer sister, so i finally take the decision to publish this new plan. the goals of this plan is simple: add interior volume, simplify the work for homebuilders switching to a complete plywood & epoxy radius chine hull, enhance slightly the sparkling performances of idea 19, keeping the sailboat very balanced and suited for sailors ranging from enthusiast beginners to experienced seamen., first boat launched and several other boats in building stage make idea21 the most sparkling project on our catalogue, hull: chined hull on a small light sailboat has a simple reason to exist: it gives more stability to the sailboat when heeled, much more than a round hull similar sailboat. i managed to keep a very low wetted area of the unheeled hull, in order to achieve a good pace in light air and avoid excessive drag. stern sections are quite flat to gain speed downwind (idea 19 has been clocked with speed steadily in excess of 15 knots)., bow sections: experiences on racers showed that “knife-blade” bows may give you less resistance, but the price to pay is high in terms of buried bow sailing downwind, so i decide to provide this plan a large u-shaped section on the bow ; sails provide the sailboat plenty of power to defeat the small amount of added drag., sailplan: i have a very good starting point with idea 19, so we’re doing small adjustments and no revolutions: square top mainsail, 7/8 fractional rig , very wide single swept spreaders, no backstay, deck stepped mast with sturdy section, 110 % j jib, code zero, jennaker hoisted on swinging retractable bowsprit, and a good amount of sail area., keel and ballast: idea21 have a solid hard wood cored & unidirectional glass epoxy laminated lifting keel, with a naca optimised profile and a low resistance hydrodynamical shaped 280 kg lead bulb bolted on the keel tip; it can be made by a homebuilder, no need for professional welder; the fin area is on the low side, speed will help generating the required lift without adding too much drag. keel case is in 20 mm thickness plywood and epoxy laminated glass reinforcements, and it’s perfectly waterproof while sailing., full lifting keel version : after a request from a builder, idea 21 cruise is available in a version featuring an integral watertight keel case running form hull bottom to cabin top panels, this feature called flk (full lifting keel) will allow the boat to sail with keel partially raised or to motor with keel totally up, a good option if you sail in shallow waters frequently., cockpit: was one of the strongest point in idea19, we simply keep the same arrangement and dimensions, so we have a really huge area for the crew and a simple and sturdy building in plywood panels epoxy glued on a structure of bulkheads and stringers., interiors: here i focussed on several upgrades; i decided to split the project in two versions (so two different sets of plans, you have to specify on order), “sport cruise” or “racing” ; both versions have 4 berths, a classic v berth on bow and two quarter berth after; in the cruising version cabin is 55 cm longer, giving wider interiors, enough room for a separate toilette and more comfortable after berths ; in the racing version we have a marine toilet (there’s room for a jabsco compact one) under the bow v-berth; cabin height is 1.65 m in both versions. interiors plywood panels are detailed on plans., taking advantage form the first season of sailing, i can now say that i strongly advice the cruise version as long as you are not going to run a sailing school, thus needing extra space in the cockpit., wooden rig: starting form summer 2019 we deliver two extra drawings with the plans, both for race and cruise version, describing how to build a wooden rig suited for this boat. keep your budget low at the price of a small extra weight , how to build the boat: we chose the plywood & epoxy resin “radius chine” system, as for petrel 28 and hirundo 750, so the hull planking is in okume marine grade plywood ; planking the hull is quite fast , and the internal structure of the boat is made by plywood bulkheads, floors and solid wood longitudinal stringers, all glued with epoxy and strengthened with epoxy laminated glass tape, assembled on a cheap wood scaffold, keeping the hull light, sturdy and quite easy to build for homebuilders ; the goal is to keep the total weight of the 19 footer, raising the ballast fraction of the sailboat at the same time. here are a couple of pictures of the first planked hull perfectly showing the radius chine planking system.
a HUGE Thanks to Nils Theurer ([email protected]) for the awesome pictures taken during the first sea trials

Plans availability: Plans are available in italian and english. Plans are available in imperial units upon request (send me a mail before purchase).

By continuing to use the site, you agree to the use of cookies. more information Accept
The cookie settings on this website are set to "allow cookies" to give you the best browsing experience possible. If you continue to use this website without changing your cookie settings or you click "Accept" below then you are consenting to this.

From the origins of cruising yachts to wood-based naval construction, until the advent of plywood-epoxy yacht building: how RM Yachts has modernized a unique building process.
What is plywood?
Plywood is a material that is currently used in different sectors, such as:
- construction
- packaging for transportation
It looks like a composite sheet, due to the superposition of crossed, 1 to 4mm thin plies of wood.
Plies are obtained after unrolling wood ridges, stoved during 12 to 72 hours depending on the essences. They are then cut, dried, glued and superposed in crossed ways, before being pressed.
The whole process for building a panel of industrial plywood can be described in twelve steps:
- Cold pre-pressing
- High temperature pressing
- Conditioning
The maximum thickness of industrial plywood is 40mm. Panels are balanced, meaning that the different plies are split in a symmetrical way. Panels are also heterogenic, hygroscopic, and orthotropic (they have different characteristics depending on the three perpendicular directions).
The crossed plies confer to the panels a greater homogeneity and a larger dimensional stability, compared to raw wood.

Plywood panels for structural use have become popular thanks to the synthetic resins in the 20 th century.
RM Yachts’ plywood-epoxy sailboat construction technique
RM Yachts has over 30 years of experience as a French sailboat manufacturer . One of the originalities of our modern cruising yachts is that they are made using plywood , which is assembled on a jig. Our plywood is made in France and comes to us from a factory which supplies laser-cut parts that are ready to assemble.
RM sailboats range in size from 9 m to 14 m, and each model has its own assembly jig on which the planks are positioned and assembled by jointing and laminating. For the vessel’s planking running the whole length of the hull, the parts are butt-jointed by means of a “scarf” joint in which the two ends of the plank are cut slantwise and overlapped, ensuring a very strong, rigid join. The time to build the hull on the jig varies from one model to another, depending on the size of the yacht.
RM boats are fitted with a metal part in the bottom which increases the rigidity of the structure and on which the different types of keels (fin keel, twin keel, or lifting keel) are subsequently mounted.
RM Yachts completes the following different stages to build a plywood-epoxy liveaboard sailing boat:
Coating the hull and shaping the bilges
Once ready on its jig, the hull is then “unmoulded” and, still upside down, moves to the assembly station where the bilges will be coated with epoxy to give the hull its shape.
Laminating the inside of the hull
Whilst the outside of the hull is coated with epoxy, structural lamination is carried out inside the sailing yacht to ensure maximum rigidity. The structural bulkheads are laminated.
Manufacture of the composite deck
RM decks are mostly made of composite produced by infusion moulding to optimise the weight. They are manufactured by the La Rochelle-based company A2J, a neighbour of RM Yachts. Composite is an excellent choice for deck construction, as this technology enables very fluid, rounded shapes to be achieved, which are characteristic of the RM Yachts monohull sailboats designed by the naval architect Marc Lombard.
Cladding and painting the inside of the deck
Whereas the interior bulkheads of our RM sailboats are laminated, and the bilges shaped by applying epoxy hull coating, the deck is given cladding on the inside.
This almost total coverage is completed using plywood, which offers excellent thermal and sound insulation, and additional rigidity. Once this operation is finished, the inside of the deck is painted in a paint booth.
Painting the inside of the hull
Whilst the cladding and paint are being applied to the deck, the hull is turned over and operations begin to install the interior fittings. This starts by the final lamination and then coating of the bulkheads. A primer is then applied before painting the inside of the hull.
Fitting out before the deck is installed
Once the inside of the hull is painted, fitting-out operations prior to installing the deck begin. At this point, the furniture modules made by a local subcontractor are fitted, together with the power and water systems and the engine. All the large or heavy fittings are now in place.
Installing the vessel’s deck can begin
Fitting the deck
The deck of an RM sailboat is installed just after the furniture, the power and water systems and the engine have been fitted in the hull. The deck fittings are mounted. The deck is then positioned and bonded onto the hull followed by lamination, a solution which contributes to the structural strength. The point where the deck meets the hull (the deck edge) is then coated with epoxy and sanded for a perfect invisible join.
Painting the hull
The next stage, lacquering the hull, is one of the longest in building an RM, requiring many different steps separated by drying times.
The RM Yachts shipyard is one of the only ones to paint the hulls of all its boats, thanks to its plywood-epoxy sailboat construction technology.
While the boat is still upside down, the bilges and laminated joints are coated with an epoxy layer. It is then sanded.
Next, a very thick primer is applied by spray gun to correct any unevenness in the surface.
A second thinner, more dilute layer of epoxy primer is then applied to finish. This epoxy “finish” flows better and improves the quality of the finished surface.
It is then sanded again.
Next, an ultra-smooth polyurethane primer is applied.
Once this layer is dry, the completely personalised bi-component polyurethane high-gloss lacquer topcoat is applied to produce the perfect cruising yacht for each customer.
Finishing and fitting the keel
Once the hull has been painted in the paint booth, the final steps can be completed to finish the inside and outside of the RM.
The portholes, interior lighting, electronic equipment, ceilings, panelling, and doors are fitted.
The very last stage before delivery is the installation of the keel. The shipyard offers three types of keels: fin keel (a single keel), twin keel, or lifting keel.
How has our building technique evolved?
Martin Lepoutre, General Manager, RM-Yachts:
“RM Yachts benefits from a unique experience and history of building sailing yachts with plywood-epoxy. Since inception, more than 500 sailboats, from 30 to 45ft, have been built here in our French shipyard, in La Rochelle.
Today, our range of modern plywood sailboats include:
Year after year, we have constantly improved our building process:
- The mannequins have been improved to make sure we can assemble the hull in the best conditions and control the transversal and longitudinal structure.
- The assembly has been improved with fillet sealing, and then the stratification of all the bondings.
- The epoxy resins we use are more and more performant, but also more environment friendly.
RM Yachts is unquestionably the shipyard with the longest experience and track record in this area. Thanks to this efficient sailboat building technology, the achievements are:
- a top quality
- incomparable solidity
- a fantastic performance/displacement ratio
Advantages of plywood-epoxy: why has Marc Lombard selected this material to build RM sailing yachts?
Interview of Marc Lombard, architect of the RM Yachts.
What are the benefits of plywood-epoxy for blue water cruising yacht building?
The benefits are not only for the blue water or expedition yachts, but for all yachts! The benefit of this technology stands in the material itself: plywood-epoxy. Wood is not a dense material and offers an interesting solidity/weight ratio. If you think the other way around, what we first need on a sailing yacht is solidity.
If you build it with plywood-epoxy, you’ll get a lighter boat than its equivalent in aluminum or GRP. If she’s lighter, it means we can build an even more solid yacht for an equivalent weight or build one with a higher load capacity.
When it comes to blue water cruising sailboats, it’s a balance between this light displacement and the ability to benefit from this extra load capacity. If you want a super solid sailboat, she’ll always be lighter than the equivalent in other materials such as iron, aluminum, or GRP.
Raw wood is a hard-to-process material. For the past 25 years, we’ve worked hard with RM Yachts to finetune this plywood-epoxy sailboat construction process and make it economically viable and competitive. It’s quite a challenge, as it costs more money compared to monolithic polyester, but it offers many more benefits in terms of solidity, lightness, and insulation.
When it comes to insulation, the first benefit is clearly a moisture-free atmosphere. There’s no mistiness with 18mm planking, while iron or aluminum would require additional insulating materials. Not to mention the easiness to repair plywood-epoxy.
(ActuNautique.com, 2016).

Marc Lombard and the sailor of the future, Voile Magazine, April 2021.
25 years ago, Marc Lombard designed the RM800. An easy to clean, easy to store, easy to live, great little boat. A seaworthy design, able to sneak in the tiny coves thank to her reduced draft, but also capable of offshore passages. In a nutshell, a yacht in which Marc Lombard put the best of himself. “At that time, the twin-keel yachts were solely English”, but he worked hard to make them more performant. Using plywood-epoxy, that he had discovered when working with Walter Green and the West System technique, he knew he was in the right direction. Since inception, RM Yachts range has evolved and the sailing yachts have become more and more performant and comfortable, yet elegant. But they have kept this original philosophy of seaworthiness. RM Yachts are made to munch miles, and their owners usually buy them for this purpose. Even if they are looking for comfort. A requirement Lombard takes seriously into account, when he reduces the number of steps in the companion way, between the cockpit and the saloon area. Not yet like a cruising catamaran, but that’s the idea behind it. RM Yachts will continue to evolve, but maybe not with foils or scow bows! Because all offshore innovations are not necessarily adaptable on cruising yachts. According to Marc Lombard, the question is not about the yachts of the future, but about the sailors of the future. What will be their expectations? What will they look after? A way to underline the fact that we have the yachts that we deserve!
A look back in history
The origins of plywood-epoxy sailboat construction.
Plywood sailing boat building started back in the 1960’s. The first naval architects to use this technique were Harlé, Herbulot or Van De Stadt. In France, they gave birth to legendary yachts such as the Muscadet or the Corsaire. Plywood was lighter, waterproof, and required less maintenance than raw wood.
Sometimes seen as an amateur, non-professional technique, with perfectible finishings, this building process has quickly evolved to finally be mastered by shipyards such as RM Yachts, thanks to Marc Lombard’s design. Today, plywood is combined with epoxy.
This combination with epoxy resin enables an even better waterproofing and facilitates maintenance. Combined with fiberglass, it becomes a fantastic material to build yachts, with a weight/resistance ratio clearly more favorable than the ones of aluminum or monolithic polyester.
The plywood-epoxy used by RM Yachts to build our cruising yachts today can be defined as a wood-composite material.
For the record, a composite material is the assembly of at least two non-miscible components, whose specifications are complementary. the material obtained by this assembly is heterogenic and offers resistance characteristics that the sole components do not have.
What is the « West System »?
Marc Lombard is one of the first naval architects to have imported in France the concept of plywood-epoxy sailboat construction. It is actually a technique that American yacht builders already mastered, thanks to the discovery of a marine-grade resin, called West System, created by the Gougeon Brothers.
The Gougeon family, originally from Chicago, IL, set up a new process: saturating a plywood panel with resin. The first application of this technique was the building of “ice-boats”, designed to navigate on the frozen waters of the great lake’s region.
They eventually designed a few sports multihulls and won a few local regattas and championships. In 1975, they decided to stop competition, and focused on the fabrication of this specific resin, aiming to sell it to other boat builders.
In 1979, they wrote a book on boat construction using plywood-epoxy. This book became the bible for many architects. It was re-edited 5 times, until 2005.

In this book, the Gougeon brothers will explain the virtues and benefits of plywood combined with epoxy, comparing it with other materials used for boat construction. Starting with solidity and rigidity.

Among the various plywood boat building processes, the one preferred by the Gougeon brothers is the “compounded” one. It consists in assembling plies, impregnated with resin, and to press them to obtain a desired given shape.
It is actually the technique that is still used nowadays at RM Yachts.
Below is the 35-footer trimaran “Ollie”, built by the Gougeon Brothers back in 1985.

A manufacturing technique that inspired many
This plywood boat construction technique will be used by Dick Newick to build his first multihulls, but also by Walter Green, in Yarmouth, Maine. Guess what? The latter will welcome the young Marc Lombard as a trainee, when working on “A Capella” for Charlie Capelle, sistership of the little yellow trimaran Olympys, commissioned by Mike Birch, winner of the Route du Rhum in 1978.
“For me, there is no other option for boat building but wood. When you come aboard a yacht, you have to feel something, an atmosphere, some emotions. In a GRP boat, this is quite hard to feel, while in a wooden boat, you’ll immediately feel a soul, a spirit, a strength. There’s something happening because it’s a material that is alive. In terms of solidity, when it is properly worked out, and well maintained, you know it will last forever. A Capella is a great example: she spent a year and a half upside down, tossed by the waves on the beach, and she is still in pristine conditions”
(Charlie Capelle, Voiles & Voiliers magazine, 2014).
About leisure sailing
No one exactly knows when the first sailing boats were used for leisure purposes. The first leisure sailors probably used a mix of sails and oars as auxiliary source of power. Since Antiquity, some ships were used for celebrations, anniversaries, and even races. Sailing on the Nile river and later on the Med has been recorded by antique Assyrian, Phoenician or Egyptian civilizations.
The origin of leisure sailing or “cruising” is more recent and has been found in the Netherlands and the UK.
In 1601, a Dutch named H. Voogt managed to get an authorization to sail from the Netherlands to London, for fun. This marks a kind of milestone in the definition of cruising. But what is the exact definition of leisure? “Use of free time for enjoyment”. That’s a good start, isn’t it?
When it comes to “cruising”, Cambridge’s dictionary says: “the activity of going on a journey on a ship for pleasure ”.
Sailing a yacht for enjoyment, could be another definition. At least, this is the one that corresponds the best to RM Yachts philosophy!
Nowadays, leisure sailing comes in many forms and liveaboard sailboats are used by couples, families and solo sailors for port-hopping, coastal cruising, bluewater sailing, ocean crossing, etc.
Sailing for pleasure is probably the best definition of yachting. At least that is how RM Yachts defines it.
About “yacht” origins.
The English word “yacht”, today commonly used to design a sailing vessel, has Dutch roots: the jaght schip was originally used in the late 16 th century. The verb jaghen meaning chasing, going after, and the word schip meaning ship or vessel. This etymology underlines the fact that the notion of a fast sailing yacht has been key to the development of leisure crafting.
Since 1989, RM Yachts continues to foster this definition: our monohull sailing yachts are fast, and comfortable!
Cruising and leisure sailing will give a second chance to sailing. In the second half of the 20 th century, this activity will be democratized. A good example of this spectacular boom is the Vaurien, an affordable and solid 13ft dinghy. Built using just one single sheet of plywood.
How were the first cruising yachts built?
It seems the construction of sailing boats was done using the materials that could easily be sourced locally. Logically, wood, easy to cut and assemble, has been mostly used in different parts of the world, until plywood and its many benefits came in.
Keep in Touch' Restons en contact
We will send you RM Yachts News (Only) to make sure you are up to date. Recevez (seulement) nos infos, pour être sûrs de ne rien rater !
- FR - Français
- EN - English
Home » LIST of WOODEN BOAT PLANS – By Michael Storer » 15 1/2 ft Rowboat Easy Build in Plywood
15 1/2 ft Rowboat Easy Build in Plywood
The Storer Rowboat is a pretty and fairly fast plywood rowboat plan that is easy to build. The shape is derived from the famous Goat Island Skiff sailboat plan which rows fast without much effort. This rowboat will be fast and responsive under oars.
Buy Rowboat Plans Here $75
Basic Dimensions of MSD Plywood Rowboat Plan
Length 15 ft 6 inches x 4ft beam Estimated weight 90lbs Plans $75 including detailed instructions
- Payload – one person – second person or a couple of children and picnic things are OK too.
- A swift rowing boat for one person – with the capability of carrying an extra person (or two if they are not toooo heavy) for fishing or picnics.
- Easy construction – but an easily driven shape that is rewarding to row.
- Large enclosed buoyancy for safety – 8ft oars no outriggers
PDF Plans by email – $75. See list of agents top left on this page or click here .
There is a report about one being built here on the OZ woodwork forums.. And now another one And another one
General Comments about the Storer Rowboat.
This design has had a very long gestation – over two years. My normal well-documented plans were around half way finished and I just couldn’t continue with this boat for oars – a sure sign there was something I wasn’t quite happy with. I scrapped the whole thing and started again a few weeks ago.
Generally I don’t design boats to order. In this case two emails from old boatbuilding friends prompted the development of this boat for oars. Initially I headed in the direction of something much more racey. But then realised that Peter and Richard wanted speed but with more flexibility.
The racey version was finally rejected when Peter asked me about where he was going to cut the bait!
So it evolved in a more sensible direction.
The front and back seats take up a lot of the boat length for a safety factor. But also to push the passengers toward the middle of the boat so the stern and bow do not drag. The middle seat is very wide so there can be two sets of rowlock sockets – front one for when there is a passenger in the back. It can be used for storage or batteries if using a electric trolling outboard.
The Never Ending Dory
For some time I had thought of using the Goat Island Skiff (GIS) design as the basis for a plywood rowboat – more slender, lighter, lower. Thus catching the wind less.
Here were the models of the GIS with the Rowboat plan prototype. Not to same scale. they are the same length.
Stability under oars
It also is a response to the number of lightweight plywood dory designs that are around these days. Old dories weighed hundreds of pounds and were around 20ft long overall and are reputed to need a good load of fish to make them into stable platforms under oars. Consequently shrink them and lighten them and the stability drops off very rapidly. This plywood Rowboat has ample.
Tom really wanted to show this to me under oars when I met him north of Newcastle for the photos.
Why we didn’t use a dory as a base for the Rowboat plan.
First of all … there are too many dory designs. Many of them nondescript.
Of the modern, shorter, lightweight dorys, the better ones of the modern kind paddle very easily but are tender until you have a load aboard and their speed under oars is limited by the short waterline. The worse ones are so twitchy as to be almost useless.
Some try to fudge a dory shape by having curved clinker sides. But then you lose the simplicity. This rowboat is not really suited to wavey oceans, though one who uses his off the coast of Maine enjoys it. Most will be used in estuaries are rivers where there is a chop.
Tom under oars.
Talking with the Row Boat Designer: The Emails from Peter
Peter wrote:
On thinking about the rowing boat brief…. n o, dash it all NO passengers, if she wants to come we’ll go in Gruff (ie the Goat Island Skiff) or the canoe! Sooo… two sheets of ply long, needs to be a bit more utilitarian than a shell, so that one can cast a line or pick up a crab pot. But really it’s a boat for the sheer pleasure of going for a row. I don’t know too much about rowing properly, but a sliding seat option may be ok?? Has to be pretty, which is why I’m keen for you to look at it! The Goat Island Skiff with a foot out of the beam??
My response: Was to say, yes, yes, yes – but Richard had slightly different criteria as far as payload.
And from Richard, the other client.
Richard wrote:
For efficient rowing on the river (Murray) – so against current, some chop, wake from power boats, but not open ocean or rough water. Come to think of it, the wake thrown up by your average yahoo driven ski boat probably qualifies for ‘rough water’. Especially as I’ll often have my little daughter in the ‘boss’s seat’. Will be used for fishing (I sit when I fish in a boat) and exploring. Cheap to build without sacrificing usability. Light – although this boat will be carried on a trailer, it will be launched and recovered from river banks, not boat ramps. Light enough to car top or for one person to carry would be nice but not essential. I’m after a tough, light, utility boat, not an ultra-light weapon. Enough floatation for safety if swamped – I’m not some panic merchant who expects it to float on its water line when full of water – just high enough to get back into.
My Response: Again – Yes. A move toward general use as Richard describes willl also make the plans more interesting to more people.
She will float a little deep with three aboard. But keeping the base of the transom narrow and shallow any bad effects will be minimal. I think she will prefer to carry three lighter individuals or a heavier adult a lighter adult and a child. Truthfully she will be at her best one up.
A Quick Model to give us an idea of the actual shape the rowboat plan was converging on
I drew up shape on the computer and emailed some panel outlines so models could be made by both interested parties – they are both experienced boatbuilders.
The photos of the plywood rowboat plan model arrived the next morning! Peter whipped it up overnight and photographed it with the red timber glowing in the morning light. The white boat is the model of the Goat Island Skiff that Peter built years ago. Scale is approximately similar.
The version that has been developed since has more side panel flare to give a larger beam for more stability and to carry 8ft oars without outriggers.
Boat Aesthetics
Both Peter and Richard were quite happy with the appearance from the model – as was I.
On double checking the dimensions and found that the bow had crept up too high – almost 500mm above the waterline – it would have caught the wind very badly – so it has been reduced but with a fraction more sheer in the stern. The wireframe drawing reflects the current shape.
Technical thinking about the Plywood Rowboat
It is interesting to compare the shape of the rowboat with the Goat Island Skiff (GIS – below) which was based around an excellent sailing performance.
You can easily see the difference in volume and height from the water.
. Both are simple hullshapes, but rowboats have much less power available.
Wetted Surface
Reduced in the plywood rowboat by narrowing the width of the bottom throughout relative to the GIS particularly in the stern. It was tempting to go toward a canoe stern, but it would sink heavily when a passenger was in the back seat. And stability would be reduced for other uses.
Bottom width
Reduced but the width at the gunwale retained to provide a good base for oars. Oar length is approximately twice the beam so if the beam becomes too small then the oars have to shrink too – for less efficiency.
Prismatic co-efficient (C P )
A measure of how much volume is in the ends of the boat. Light sailing boats like the sail powered GIS can easily average 6 to 8 knots so need extra volume in the stern and bow at speed. The plywood rowboat will only ever get up to around 3.5 to 4 knots so the C P needs to be lower. It was hard to achieve the exact numbers required because of the transom width so we have gone as far as possible. Getting rid of the passenger and having a canoe stern would make it easier to get the right numbers.
It ends up looking quite a delicate little thing.
Naming Rights
The MSD Rowing Skiff is a rowing boat derived from the Goat Island Skiff with less beam and less windage making it nicer as a wooden rowboat.
I haven’t come up with the right name for this boat yet so it remains the MSD Rowing Skiff. It actually fits nicely within my range – some people build the Goat Island Skiff to serve as a rowboat where it is more than adequate when fitted with a skeg. But where less capacity, more speed for the same effort and the ability to cartop (narrower and lighter) is more important the Rowing Skiff will be more suitable. Plans are $75 and the boat will use up 4 sheets of 6mm ply. Agents listed top left of every page.
WOODEN BOW TIES
How to build a wooden sailboat: a beginner's guide.
Are you interested in building your own sailboat? If so, building a wooden sailboat can be a rewarding and fulfilling experience. Not only will you have a unique vessel to call your own, but you’ll also learn valuable woodworking skills along the way.
To get started, you’ll need to gather the necessary materials and tools. This may include oak plywood, epoxy resin and hardener, thickener, brad nails, masking tape, a pull-saw, and a table saw. Once you have everything you need, you can begin the process of building your sailboat. From creating a jig and frame assembly to making the mast, there are many steps involved in building a wooden sailboat. But with patience and attention to detail, you can create a beautiful and functional vessel that will bring you joy for years to come.
Understanding the Basics of a Wooden Sailboat
If you are interested in building a wooden sailboat, it’s important to understand the basics of how a sailboat is constructed. In this section, we’ll cover the parts of a wooden sailboat and the different types of wooden sailboats.
Parts of a Wooden Sailboat
A wooden sailboat is made up of several parts, each with its own unique function. Here are some of the most important parts:
- Hull : The hull is the main body of the boat. It is the part of the boat that sits in the water and provides buoyancy.
- Keel : The keel is a long, narrow fin that extends down from the bottom of the hull. It helps to keep the boat from capsizing by providing stability.
- Rudder : The rudder is a flat piece of wood or metal that is attached to the back of the boat. It helps to steer the boat.
- Mast : The mast is a tall, vertical pole that supports the sails.
- Sails : The sails are large pieces of fabric that are attached to the mast and other parts of the boat. They catch the wind and propel the boat forward.
- Boom : The boom is a horizontal pole that is attached to the bottom of the mast. It helps to control the shape of the sail.
Types of Wooden Sailboats
There are many different types of wooden sailboats, each with its own unique characteristics. Here are some of the most common types:
- Dinghy : A dinghy is a small sailboat that is typically used for recreational sailing or racing.
- Sloop : A sloop is a sailboat with a single mast and a fore-and-aft rig.
- Ketch : A ketch is a sailboat with two masts, with the main mast taller than the mizzen mast.
- Yawl : A yawl is a sailboat with two masts, with the mizzen mast located aft of the rudder post.
When choosing a type of wooden sailboat to build, it’s important to consider your needs and experience level. A dinghy is a good choice for beginners, while a ketch or yawl may be more suitable for experienced sailors.
By understanding the basics of a wooden sailboat and the different types available, you can make an informed decision about which type of boat to build.
Choosing the Right Materials
When building a wooden sailboat, choosing the right materials is crucial to ensure the boat’s durability and performance. In this section, we will discuss the two most important materials you’ll need to choose: wood and sails/rigging materials.
Selecting the Right Wood
Choosing the right type of wood for your sailboat is critical. You want a wood that is strong, lightweight, and resistant to rot and decay. Some of the most popular types of wood used in sailboat building include:
- Cedar: Lightweight and easy to work with, cedar is an excellent choice for planking and decking.
- Mahogany: Strong and durable, mahogany is often used for building frames and keels.
- Oak: A dense and hard wood, oak is commonly used for building frames and planking.
When selecting your wood, make sure it is free of knots, cracks, and other defects that could weaken the boat’s structure. You should also consider the wood’s grain pattern, as this can affect the boat’s strength and appearance.
Choosing Sails and Rigging Materials
The type of sails and rigging materials you choose will depend on the type of sailboat you’re building and your sailing needs. Some of the most common materials used in sail and rigging construction include:
- Dacron: A strong and durable synthetic material, dacron is commonly used for sailcloth.
- Nylon: Lightweight and flexible, nylon is often used for spinnaker sails.
- Stainless Steel: Strong and corrosion-resistant, stainless steel is commonly used for rigging hardware.
When selecting your sails and rigging materials, consider the conditions you’ll be sailing in and the type of sailing you’ll be doing. For example, if you’ll be racing, you may want to choose lightweight sails and rigging materials that will help you achieve maximum speed. On the other hand, if you’ll be cruising, you may want to choose more durable materials that can withstand rougher conditions.
By choosing the right materials for your wooden sailboat, you can ensure that your boat is strong, durable, and performs well on the water.
Designing Your Sailboat
Before you start building your wooden sailboat, you need to design it. This will involve creating a blueprint and determining the size and shape of your boat.
Creating a Blueprint
Creating a blueprint is an essential step in designing your sailboat. It will help you visualize your boat and ensure that you have all the necessary components in place. You can create a blueprint using software such as AutoCAD or SketchUp, or you can draw it by hand.
When creating your blueprint, consider the following:
- The length, width, and height of your boat
- The position of the mast and sails
- The location of the rudder and keel
- The number of cabins and their layout
- The placement of any storage compartments or equipment
Determining the Size and Shape
The size and shape of your sailboat will depend on several factors, including your budget, the type of sailing you plan to do, and the number of people who will be on board.
Consider the following when determining the size and shape of your sailboat:
- The type of sailing you plan to do (coastal cruising, racing, etc.)
- The number of people who will be on board
- The amount of storage space you will need
- The amount of deck space you will need
- Your budget
Once you have determined the size and shape of your sailboat, you can start gathering materials and building your boat.
Building the Hull
When building a wooden sailboat, the hull is the most important part of the boat. It is the main structure that holds everything together and keeps the boat afloat. Building the hull requires cutting and assembling the wooden frame.
Cutting the Wood
To begin building the hull, you will need to cut the wood into the appropriate sizes and shapes. The wood should be cut according to the plans or blueprints that you have created. You can use a saw or a jigsaw to make the cuts.
It is important to use high-quality wood that is free of knots or other defects. The wood should be strong enough to withstand the pressure and weight of the water. Common types of wood used for building a wooden sailboat include cedar, oak, and mahogany.
Assembling the Frame
Once you have cut the wood, you can begin assembling the frame of the hull. The frame is made up of vertical pieces of wood called frames, which hold the shape of the boat. The frames are attached to the keel, which is the main structure that runs down the center of the boat.
To assemble the frame, you will need to use a sawhorse or other support to hold the lumber in place. You can then use screws or bolts to attach the frames to the keel. It is important to ensure that the frames are level and straight.
After the frames are attached to the keel, you can add the planks to the hull. The planks are attached to the frames and keel using screws or nails. It is important to ensure that the planks are properly aligned and spaced.
Once the planks are attached, you can sand and finish the hull to give it a smooth and polished look. This will also help to protect the wood from the elements.
Building the hull of a wooden sailboat requires patience and attention to detail. With the right tools and materials, you can create a strong and beautiful hull that will last for years to come.
Installing the Deck and Cabin
Installing the deck and cabin of your wooden sailboat is a crucial step in the construction process. It not only adds to the aesthetics of your boat but also provides structural support. Here are some tips to help you through the process.
Deck Installation
The deck of your wooden sailboat should be installed after the hull has been completed and before the cabin is built. It is important to ensure that the deck is watertight to prevent any leaks. Here are the steps to follow when installing the deck:
- Cut the deck to fit the hull and sand the edges to ensure a tight fit.
- Apply a layer of epoxy to the hull and deck joint to seal it.
- Secure the deck to the hull using screws or bolts.
- Apply a layer of fiberglass cloth and epoxy to the deck to make it watertight.
- Sand the surface of the deck to prepare it for painting or varnishing.
Cabin Installation
The cabin of your wooden sailboat provides shelter and storage space. It is important to ensure that it is properly installed to prevent any leaks. Here are the steps to follow when installing the cabin:
- Build the cabin on a flat surface using marine-grade plywood.
- Cut the cabin to fit the deck and hull and sand the edges to ensure a tight fit.
- Apply a layer of epoxy to the cabin and deck joint to seal it.
- Secure the cabin to the deck using screws or bolts.
- Apply a layer of fiberglass cloth and epoxy to the cabin to make it watertight.
- Install any windows, hatches, or doors in the cabin.
- Sand the surface of the cabin to prepare it for painting or varnishing.
By following these steps, you can ensure that your wooden sailboat’s deck and cabin are properly installed and watertight. This will not only make your boat look great but also ensure that you have a safe and enjoyable sailing experience.
Setting Up the Mast and Sails
Now that you have built your wooden sailboat, it is time to set up the mast and sails. This process may seem daunting, but with a little patience and attention to detail, you can have your boat ready to sail in no time.
Step 1: Install the Mast
The first step is to install the mast. Depending on the design of your boat, the mast may be a single piece or assembled from multiple sections. Make sure the mast is secured properly and is straight. Use a level to ensure the mast is vertical in both directions.
Step 2: Prepare the Sails
Next, prepare the sails. Make sure the sails are clean and free of any debris or damage. Attach the sail to the mast using the halyard, which is a rope used to raise and lower the sail. Make sure the sail is hoisted all the way to the top of the mast.
Step 3: Attach the Boom
Attach the boom to the mast and secure it with a boom vang, which is a rope used to control the angle of the boom. The boom is the horizontal spar that holds the bottom edge of the sail.
Step 4: Set the Sail
Once the boom is attached, set the sail. Adjust the angle of the boom and the sail to catch the wind and start moving. You can use the main sheet to control the angle of the sail and the boat’s speed.
Step 5: Trim the Sail
Finally, trim the sail to optimize its performance. This involves adjusting the sail’s shape and position to maximize its power and minimize drag. Use the sail controls, such as the cunningham and outhaul, to adjust the sail’s shape. Use the main sheet to control the sail’s position relative to the wind.
Congratulations! You have successfully set up the mast and sails of your wooden sailboat. Now it’s time to hit the water and enjoy the thrill of sailing.
Applying Finishing Touches
When it comes to building a wooden sailboat, applying the finishing touches is a crucial step that can make all the difference in the final product. Here are some tips and tricks to help you get the perfect finish.
Sanding and Finishing
Before you can apply any finish, you need to make sure the surface is smooth and free of imperfections. This means sanding the wood with progressively finer grits of sandpaper until you achieve the desired smoothness. Once you’ve finished sanding, you can apply a wood conditioner to help the wood absorb the finish more evenly.
When it comes to choosing a finish, you have several options. Some popular choices include varnish, paint, and oil. Varnish is a popular choice for wooden boats because it provides a durable, glossy finish that can withstand the harsh marine environment. Paint is another option, but it requires more maintenance than varnish and may not provide as much protection against the elements. Oil is a good choice if you want a more natural look, but it may not provide as much protection as varnish or paint.
Painting and Varnishing
If you decide to go with paint or varnish, there are a few things to keep in mind. First, make sure you apply the finish in a well-ventilated area to avoid inhaling fumes. Second, make sure you apply thin, even coats and allow each coat to dry completely before applying the next. This will help prevent drips and ensure a smooth finish.
When it comes to varnishing, it’s important to use a high-quality brush and work quickly to avoid brush marks. You may also want to consider using a foam brush for hard-to-reach areas. Once you’ve applied the final coat of varnish, you can buff the surface with a soft cloth to achieve a high-gloss finish.
Painting requires a different approach. You’ll need to choose the right type of paint for your boat and make sure you apply it evenly. If you’re painting a large area, you may want to consider using a paint sprayer to achieve a smooth, even finish. Once the paint has dried, you can apply a clear coat to protect the paint and give it a glossy finish.
In conclusion, applying the finishing touches to your wooden sailboat is an important step that requires careful attention to detail. By following these tips and using the right tools and materials, you can achieve a beautiful, long-lasting finish that will protect your boat and make it stand out on the water.
Safety Measures
When building a wooden sailboat, safety should always be your top priority. Here are some safety measures you should take to ensure a safe and successful build.
Installing Safety Equipment
Before you start building, make sure you have all the necessary safety equipment installed in your workshop. This includes fire extinguishers, smoke detectors, and first aid kits. You should also have a clear and unobstructed path to the exit in case of an emergency.
When working with power tools, always wear eye and ear protection, as well as a dust mask to protect your lungs. If you are using chemicals, make sure you are working in a well-ventilated area and wear gloves and a respirator if necessary.
Conducting a Safety Check
Before you start working on your sailboat, conduct a safety check to make sure everything is in order. Check that all tools and equipment are in good working order and that there are no loose or damaged parts. Make sure your work area is clean and free of clutter, and that all cords and cables are properly secured.
When working with wood, be aware of any knots or cracks in the wood that could weaken the structure of your sailboat. Use only high-quality marine-grade wood and be sure to follow the plans carefully to ensure a strong and safe boat.
By following these safety measures, you can ensure that your wooden sailboat build is a safe and enjoyable experience.
Maintaining Your Wooden Sailboat
Congratulations on building your own wooden sailboat! Now that you have a beautiful vessel, it’s important to keep it well-maintained to ensure its longevity and safety on the water.
Regular Maintenance
Regular maintenance is essential to keep your wooden sailboat in top condition. Here are some tips to keep in mind:
- Clean your boat regularly with a mild soap and water to prevent dirt and grime buildup.
- Check for any signs of damage, such as cracks, rot, or loose fittings, and address them promptly.
- Apply a fresh coat of varnish or paint every few years to protect the wood from the elements.
- Keep your boat covered when not in use to protect it from the sun and rain.
Seasonal Maintenance
In addition to regular maintenance, there are also some seasonal tasks that you should perform to keep your wooden sailboat in top condition:
- At the beginning of the season, inspect the hull for any damage or wear and make any necessary repairs.
- Check the rigging and sails to make sure they are in good condition and make any necessary repairs or replacements.
- Before storing your boat for the winter, make sure to properly winterize it to protect it from the cold and moisture.
Additional Tips
Here are some additional tips to keep in mind when maintaining your wooden sailboat:
- Use high-quality marine-grade products when cleaning and maintaining your boat.
- Avoid using harsh chemicals or abrasive materials that can damage the wood.
- Regularly check the bilge for any water buildup and pump it out as needed.
- Keep your boat well-ventilated to prevent moisture buildup and mold growth.
By following these tips, you can keep your wooden sailboat in top condition and enjoy many years of safe and fun sailing.
Leave a Reply Cancel reply
You must be logged in to post a comment.
How to Build a Boat: PM Constructs a 10-Foot Dinghy (With Plans)
A few months ago, home editor Roy Berendsohn tried his hand boat-building, making a 10-foot dinghy using old Popular Mechanics plans from 1937, hand tools and a cramped garage.
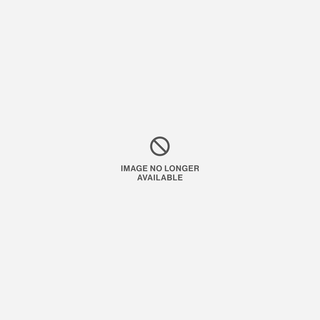
It was a long time since anyone in my family had built a boat. The last was my Uncle Paul. He was a shipbuilder who learned his trade beginning at age 14 in Hamburg, Germany. Every morning, the boy rowed from the family's dock out across the shipping lanes of the Elbe River, which flows into the North Sea. The trip to the shipyard where he was apprenticed took an hour and a half, longer in winter, when there was fog and floating ice on the water. After three years, Paul received a journeyman's certificate and a berth aboard a gigantic four-masted windjammer named Passat--"trade wind" in English. That was in the 1920s, be-fore the fascists confiscated his family's own small shipyard and the Berendsohns left for America.
A few months ago, I decided to try my hand at the ancestral trade. I've built everything from houses to a blacksmith's forge (March 2009), but there's no more evocative project than a boat, at least to me. Since before Austronesians first gazed across the Pacific, wooden vessels have stood for craftsmanship and the drive to explore. I sifted through PM's archives looking for a classic design and eventually settled on a 10-foot dinghy from our May 1937 issue. It looked elegant, yet simple enough to build on a pair of sawhorses.
It's been many years since my Uncle Paul was around to lend advice, so I ran the drawings past Timo White, a boatbuilder at Tuckerton Seaport, a small maritime museum on the New Jersey coast. It turned out that Timo was in the midst of restoring a surfboard built from plans in the July 1937 issue of PM. (It was a big year for seafaring projects, I guess.) He confirmed that the dinghy was a good candidate for a first-time builder and agreed to lend a hand if needed.
Shipyard in the Driveway
On a wintry early spring morning I set out for Willard Brothers Woodcutters, a sawmill and lumber dealer in Trenton, N.J. You can spend hours there, roaming stacks of delicious-looking walnut, cherry and oak, some of the boards as wide as your arm is long. I bought red oak for the Sea Scout's frames (that was the name of the craft in the plans, and I chose to keep it) and a 2-inch-thick slab of white oak for the wedge-shaped stem at the bow.
Back home, I started making a racket feeding planks through a table saw. My skills were creaky--I've spent too much time in recent years fixing stuff and not enough building--but over a few days my old confidence returned. The Sea Scout began to take form.
Most boats begin with the frames, the ribs that provide structure to the hull. I roughed them into shape, along with the stem and the gracefully shaped stern wall, or transom, which I cut from ¾-inch plywood. Then I braced it all to a building board--which is nothing more than a 2 x 10 with a chalk line marked down the center. The boat's skeleton was in place, but each member still needed to be precisely beveled before I could secure the curved planks of the hull. The next step was to clamp thin strips of wood, called battens, to the frame to stand in for the planks, so I could measure and mark all those angles. Then, I took the parts off the board and finished shaping them.
Often, the weather confined me to the garage, but when the sun emerged I worked in the driveway. If you want to get to know the neighbors, start building a boat. Linda from next door asked whether the craft would be sailed, rowed or powered by an outboard motor. Others wondered where I would go with it, how I'd get it there and what I would name it. A truck driver from Tulnoy Lumber, dropping off some marine plywood, approached respectfully. "This is beautiful," he said, with an old-fashioned New York accent as broad as the hand he ran over the frames.
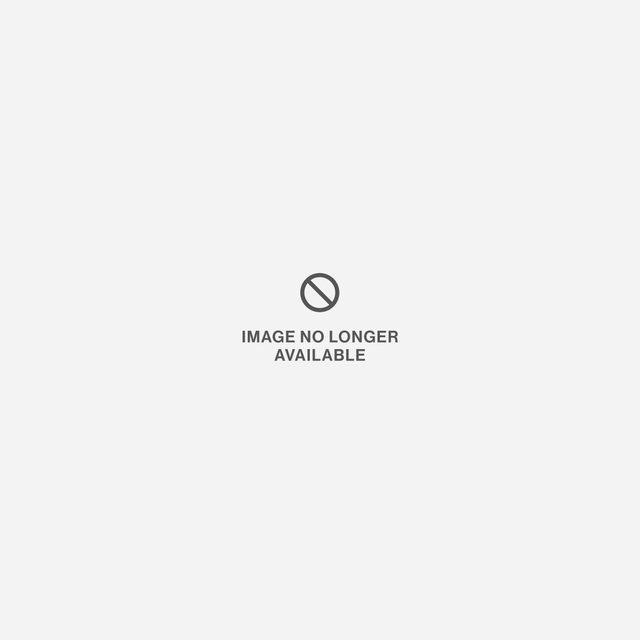
Anatomy of a Boat

1. Building Board: Like most small wooden boats, the Sea Scout was built bottom side up. Most pieces aren't permanently connected until relatively late in the process, but every element of the frame had to be shaped to fit together precisely. The 12-foot-long building board, made from a 2 x 10, held the parts in the right positions while the bevels were measured and again when it was time to join the frames together with the chine logs and planking.
2. Bottom Member: The frames underlying the dinghy's hull were fashioned from red oak. The curved section is the bottom member--each one was cut with a jigsaw and smoothed using a block plane.
3. Side Member: The gently tapered oak side members meet the bottom members at a slight angle. These pieces are cut oversize, then shortened to finished length.
4. Gusset: The gussets joining the bottom and side framing members are cut from oak and fastened with epoxy and bronze screws, some of which ended up being too close to the gusset's edge.
5. Cross-Spall: Cross-spalls support each frame during the building process. They're screwed to the side members and the building board. After the planking is done, the boat is turned upright and the supports are removed.
Working the Plank
I don't know how Uncle Paul felt about it, but boatbuilding can be acutely frustrating. The bane of my weekends proved to be a small bronze screw. A No. 6 Frearson flat-head, to be exact. Like most modern DIYers, I'd been spoiled by drywall screws and other aggressive fasteners that practically plow into the lumber. Even using a specialized, tapered drill bit and a waxlike lubricant with the unlikely name of Akempucky, I managed to wreck screws by the dozen. The head on one would strip a moment before the screw was fully seated, while another would shear off on the last eighth of a turn, leaving me with a shiny Frearson-head penny.
Timo had tried to downplay the arcana I'd face--"It's more like house carpentry than fine-furniture building," he had said--but I still found myself floundering on occasion. One challenge was that the 1937 article was more an overview than a detailed set of plans. And, though it pains me to find fault with my forebears at Popular Mechanics, the sketch contained suspicious discrepancies. Timo helped me recalibrate some of the dimensions midway through the project--and I had to trim several pieces after they were assembled.
The biggest hurdle came when it was time to plank the hull. The classic way is to bend strips of solid wood to the frames. I'd chosen marine-grade fir plywood instead to save time, but now I was barely able to force the hull's 14-inch sheets into place. There was no way the half-inch plywood I'd planned for the bottom was going to work.
Timo advised me to switch to a special, wafer-thin marine-grade plywood and plank the bottom in two layers. He came swooping in one Thursday morning to show me the technique. He stepped out of his truck with a broad smile, and a block plane in each hand, and my mood lifted. He politely took a sighting down the chine logs where we'd attach the bottom, and spent a few minutes planing them to the last measure of precision. Then we got to work with staples, glue and screws--and in a couple of hours the project went from a plywood flower bed to a small craft with sensuous compound curves.
It was satisfying, but my mistakes still showed in details like the placement of screws and the shape of the stem. "You know what they say," Timo told me. "Putty and paint makes a boat what it ain't." I got out my paintbrushes.
1. Very few elements in a boat are simply cut to shape and installed. Like the oak stem shown here, nearly every piece needs to be beveled or curved to fit the surface it meets. (That tool is a fore plane I own, built by Stanley Tools in 1927.)
2. Ancient terms persist in boatbuilding. This curving wood piece, where the bottom is attached, is called a chine log. In past centuries, it consisted of a single log chosen for its natural curve, then shaped to fit. The chine log is set in a notch and fastened to each frame.
3. Two layers of okoume plywood form the bottom of the Sea Scout. Timo (foreground) showed me how to install them.
4. The Sea Scout motored along nicely, powered by this 2.5-hp four-stroke Mercury Marine outboard.
Maiden Voyage
We launched the boat at Tuckerton Seaport on a cool, overcast day that felt more like September than June. Down at the dock, Timo produced a can of Amstel Light in lieu of champagne. "Go ahead," he said, "pour it over the bow." I popped it open and emptied the beer over the paint. "I christen thee Sea Scout," I said. Then we slid the little craft off the dock and into the water.
You might think a feeling of triumph came over me. Not so. The Sea Scout looked very small, almost helpless, as she sat bobbing at the end of the painter, the little rope that Timo had threaded across the bow. I felt humbled. A phrase from the Book of Psalms flashed in my mind: "They that go down to the sea in ships, that do business on great waters."
I wasn't aiming for any great waters myself. I eased off the dock and into the boat. Timo handed me the oars. Awkwardly, I drew the handles back, just above my hips. The craft slid forward gracefully, almost like she was on ice. As Timo watched, I braced the left oar down in the water and swept the surface with the right. The Sea Scout pivoted neatly, unexpectedly elegant and spry.
If the oars were a kick, you can imagine the thrill I felt when I mounted the 2.5-hp Mercury Marine outboard on the transom. It's a clean-running four-stroke engine, compact yet almost zippy on a boat this small. I gave the engine full throttle and cut some nice straight lines and a pleasingly tight curve complete with a crisp little wake.
With the afternoon gone, my first voyage was complete. In the end, I decided to donate the boat and engine to Tuckerton Seaport. Frankly, I needed the space in my garage and driveway: The Sea Scout was a good first foray into wooden boatbuilding, but I knew I could do better--and I'm already sifting through plans.

Roy Berendsohn has worked for more than 25 years at Popular Mechanics, where he has written on carpentry, masonry, painting, plumbing, electrical, woodworking, blacksmithing, welding, lawn care, chainsaw use, and outdoor power equipment. When he’s not working on his own house, he volunteers with Sovereign Grace Church doing home repair for families in rural, suburban and urban locations throughout central and southern New Jersey.
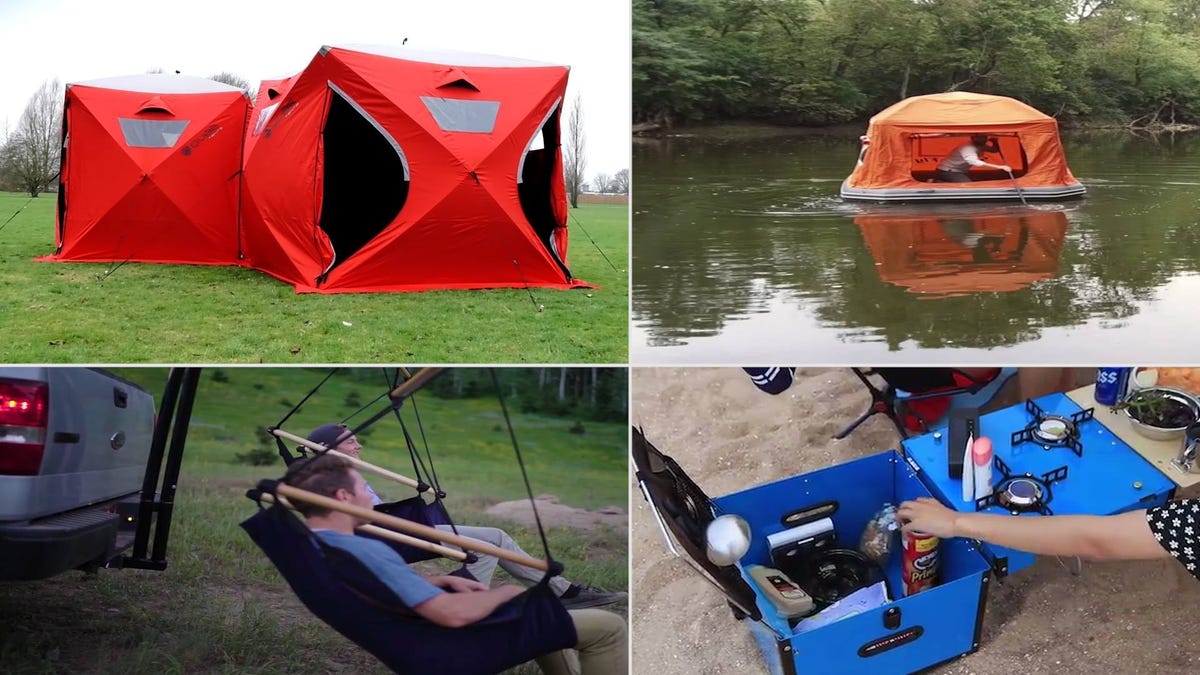
.css-cuqpxl:before{padding-right:0.3125rem;content:'//';display:inline;} Ask Roy .css-xtujxj:before{padding-left:0.3125rem;content:'//';display:inline;}
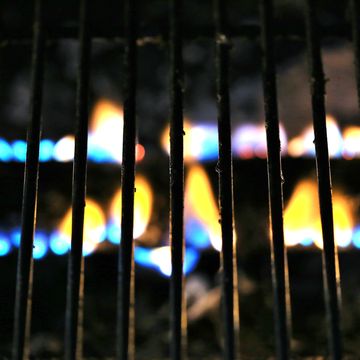
How to Stain Pressure-Treated Wood
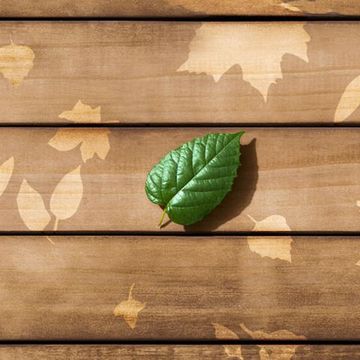
How To Get Leaf Stains Off Your Wood Deck
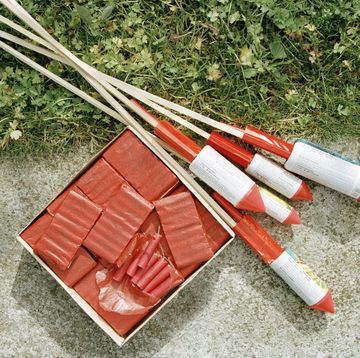
Are Bottle Rockets a Serious Fire Danger?
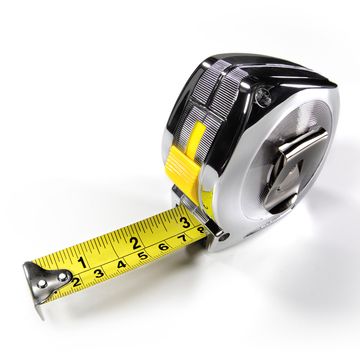
How To Cut Drywall With a Tape Measure and Knife
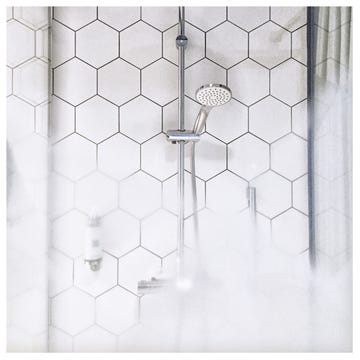
What Causes That Condensation on my Ceiling?
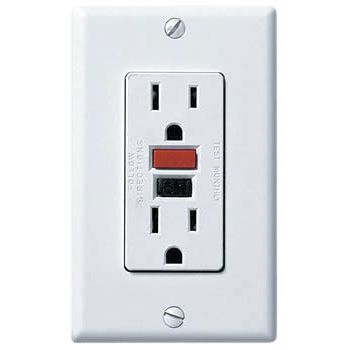
What You Need to Know About GCFI Outlets
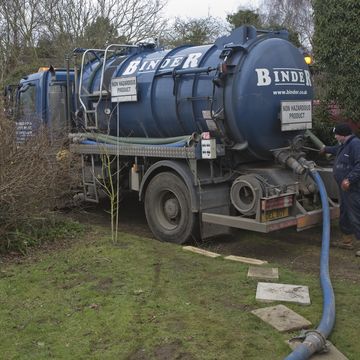
How Often to Pump a Septic Tank
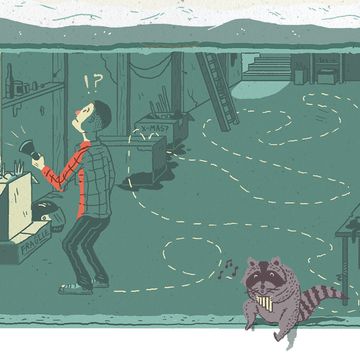
What Is This Thumping Noise in My House?
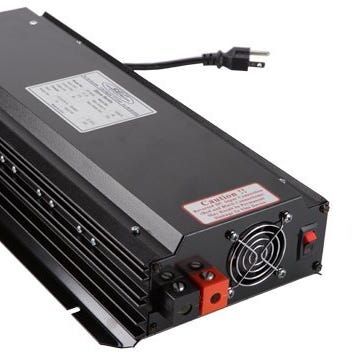
Backup Generator, or Backup Battery?
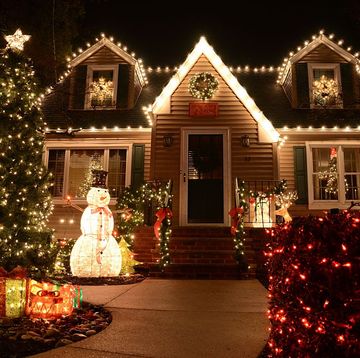
Why Your Christmas Lights Are Flickering
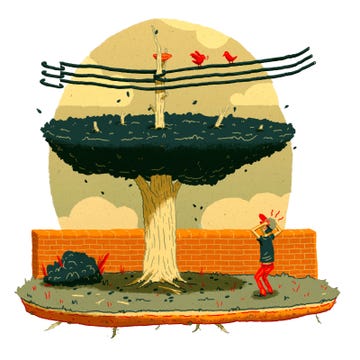
Can the Power Company Trim Your Trees?

IMAGES
VIDEO
COMMENTS
Building an 11ft Plywood Boat from start to finish using the Stitch and Glue method. Pointing out mistakes and how to avoid them.BOAT PLANS: https://plywood...
After a short break, Lou is back at it! 23' V-Bottom sea trials and new ORCA episodes on the way but first we want to share with you a great video from our ...
1. Decide which body of water you will be using the boat on. Then choose an appropriate boat design for this body of water. You will never have a boat that will do everything, so don't even try. Don't build a 24' Tolman Alaskan Skiff expecting to use it on a small lake, Midwest river, or pond.
How to Build a Wood Sailboat: I've been wanting to combine my two favorite hobbies - woodworking and sailing for a long time, so I thought I'd build a boat. ... (3/8") plywood, but I wanted to make everything out of 1/4" plywood so the thicker parts in the plans were glued together with two layers of 1/4" (so at 1/2" they were a bit thicker ...
Check out the entire build from start to finish https://www.youtube.com/watch?v=ffqGlmK6tUgBuilding a Plywood Boat | Part 1 Building the HullHANDIY Projects ...
When building a wooden sailboat, it is important to pay attention to every step, including the installation of the cabin and interior features. To install these features, follow the following steps: 1. First, measure and cut the materials for the cabin walls, floor, and ceiling. 2.
The Ultimate 5-Day DIY Plywood Boat Build. When Jason Hibbs of Borbon Moth Woodworking and Michael Alm of Alm Fabrications asked TotalBoat for support during their 5-day, no-real-plan boat build, we knew we needed to send a lot of Thixo Fast and also that we might have our hands full. These two talented woodworkers could create intricate plans ...
The sailboat hull can be constructed in a step-by-step process. Here is how you can construct a strong and durable sailboat hull: Step 1. Create the hull mold: Start by building a robust and long-lasting frame that accurately represents the shape and size of the hull. Step 2.
Step 3: Cut and Add Beams. The boat had to be strong enough to keep out 6 cubic feet of water (a cubic foot of water weighs 64 lbs), but light enough to portage short distances. And it had to withstand collisions with branches and rocks. 1x4 beams provided this strength. Cutting these was a matter of guesswork.
For most amateurs, plywood is the material of choice. Plywood is one of the cheapest and easiest building materials, one that the average do-it-yourselfer is both familiar and comfortable with. Plywood is also, pound for pound, stronger than steel. Because of its high strength to weight, plywood construction yields a boat that is much lighter […]
It's a pretty simple and quick build. The boat is made from just one sheet of cheap construction plywood. I made a little video of the build if you want to see the process in moving pictures too. Video of the one sheet plywood boat. Tools used. circular saw ; jig saw (optional) drill (with a drill and countersink bit) impact screw driver
A compilation of the 30 weeks I spent building my Goat Island Skiff . Yes, a plywood sailing boat full build!from lofting to cutting and coating the panels w...
Steps to Build a Plywood Boat. 1. Determine the kind of boat you want. The first step is to plan your boat-building project. Determining the kind of boat you want, such as a plywood fishing boat, will make it much easier to plan everything else. Decide on what body of water you'll want your boat to traverse, its size, and what you want to ...
Plywood Boats to Build Yourself - by Dudley Dix Yacht Design. Plans for building a plywood boat in your garage, build methods for beginners to experienced builders.
Idea 21 small sailboat plan is the latest development of my family of small plywood & epoxy sailboats plans for homebuilders: it was quite a time since I was thinking of an evolution of her smaller 19 footer sister, so I finally take the decision to publish this new plan. The goals of this plan is simple: add interior volume, simplify the work for homebuilders switching to a complete plywood ...
Light on the gas and light on building materials. Revised wooden boat plan for an extremely economical, efficient low horsepower riverboat. 35ft. 1 x 15hp or 2 x 10/15hp. Simple Prefab Plywood Construction. Find out more about the TC35 River Cruiser Plywood boat plan.
RM Yachts' plywood-epoxy sailboat construction technique. RM Yachts has over 30 years of experience as a French sailboat manufacturer. One of the originalities of our modern cruising yachts is that they are made using plywood, which is assembled on a jig. Our plywood is made in France and comes to us from a factory which supplies laser-cut ...
Update: We now have plans for this boat build. They can be purchased at www.thegarageengineer.com/plansWatch entire playlist of Boat build and engine repair:...
The Storer Rowboat is a pretty and fairly fast plywood rowboat plan that is easy to build. The shape is derived from the famous Goat Island Skiff sailboat plan which rows fast without much effort. This rowboat will be fast and responsive under oars. Buy Rowboat Plans Here $75.
Here are the steps to follow when installing the cabin: Build the cabin on a flat surface using marine-grade plywood. Cut the cabin to fit the deck and hull and sand the edges to ensure a tight fit. Apply a layer of epoxy to the cabin and deck joint to seal it. Secure the cabin to the deck using screws or bolts.
DIY Small Plywood Sailboat build. How to Stitch and Glue methodA short overview of the building a plywood sailboat by stitch and glue method.Construction tim...
The 12-foot-long building board, made from a 2 x 10, held the parts in the right positions while the bevels were measured and again when it was time to join the frames together with the chine logs ...
Build CROW, a unique 15' 8" Camp Cruising Sailboat built from cheap ply and lumber from the local building supply, made a very cool boat! Visit RoyDesignedTh...